Ottimizzazione della resistenza meccanica di parti stampate e assemblate
Stanley Engineered Fastening US
Barton Lin, ingegnere capo presso il team di supporto tecnico, Moldex3D
Da oltre 40 anni, STANLEY Engineered Fastening ha rivoluzionato le tecnologie di fissaggio e assemblaggio per una varietà di settori.
Oltre allo sviluppo di elementi di fissaggio che risolvono in modo univoco i problemi di assemblaggio, STANLEY Engineered Fastening fornisce anche strumenti e processi di installazione estremamente convenienti.
Sintesi
In genere, il progetto degli elementi di fissaggio fornisce dimensioni più ridotte e il controllo delle variazioni in produzione è semplificato.
Tuttavia, quando sono necessarie parti più grandi e complesse, il team ha bisogno di uno strumento che possa aiutare a prevedere tali variazioni per superare i difetti di stampaggio, come deformazioni e esitazioni o mancati riempimenti, nel processo di stampaggio a iniezione.
In questo caso, il team è stato incaricato di realizzare un sistema di iniezione ottimale per la parte di protezione.
Sfide
Per determinare la posizione dell'otturatore per prestazioni ottimali ed evitaremancati riempoimenti e/o zone di esitazione critiche.
Soluzioni
STANLEY Engineered Fastening ha utilizzato Moldex3D per analizzare le iterazioni di progettazione nelle prime fasi dello sviluppo del prodotto utilizzando il modulo esperto avanzato DOE (Design-Of-Experiment).
Attraverso i risultati della simulazione, il team è stato in grado di determinare il numero ottimale di otturatori e anche le posizioni corrette degli otturatori per la parte.
Moldex3D ha anche aiutato il team Stanley a ottimizzare la progettazione del sistema a canale freddo, che non solo ha permesso di risparmiare denaro speso per gli otturatori delle valvole, ma ha anche ottenuto un riempimento bilanciato.
Benefici
•Individuazione delle posizioni di gate ottimali in fase di progettazione iniziale dell'utensile
•Riduzione dei costi di rilavorazione e rispetto dei tempi
•Eliminazione dei difetti di riempimento
Argomento di studio
Sulla base delle migliori pratiche di progettazione, dovrebbe esserci un gate ogni 120 mm per garantire un flusso corretto.
Inizialmente, STANLEY Engineered Fastening ha selezionato tre otturatori, ma era necessario determinarne la corretta posizione per ottenere prestazioni ottimali.
Durante lo stampaggio a iniezione della plastica, il processo di riempimento è molto critico.
Il rischio di mancato riempimento si verifica se non vengono selezionati punti di iniezione corretti.
Per superare questo problema, il team di STANLEY ha utilizzato Moldex3D verificando il contributo di ogni gate e ha regolato di conseguenza le loro posizioni. Dopo aver eseguito alcune iterazioni con Moldex3D, il team ha deciso il numero ottimale di otturatori (3) e le posizioni ottimali degli otturatori come mostrato nelle Fig. 1 e 2.
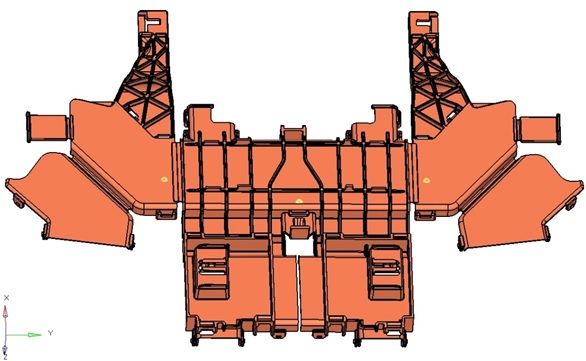
Fig. 1 Scelta iniziale del sistema di alimentazione (gate comandato)
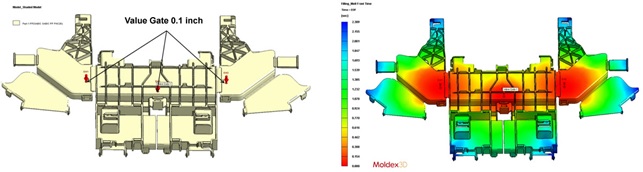
Fig. 2 Sistema di iniezione iniziale (otturatori) e risultato temporale (fronte della massa fusa)
A causa dell'alto costo degli otturatori, il cliente ha richiesto una soluzione più economica.
Pertanto, il team STANLEY, con l'aiuto di Moldex3D, ha cercato di trovare un sistema di alimentazione con un flusso più equilibrato.
La Fig. 3 mostra che la distanza dall'ingresso della materozza al Gate 2 è molto più breve rispetto ai Gate 1 e 3.
Pertanto, hanno progettato un sistema di guide in modo tale che il fuso plastico entri nello stampo dai tre gate contemporaneamente. I risultati della simulazione del fronte di fusione del sistema di gate ottimizzato sono mostrati in Fig. 4.
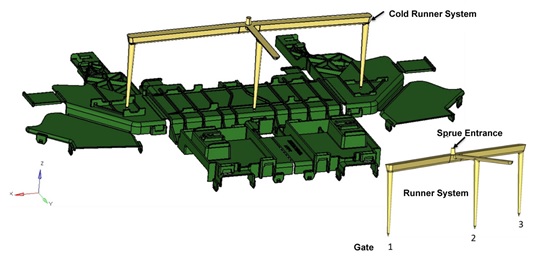
Fig. 3 Il sistema ottimale a canale freddo
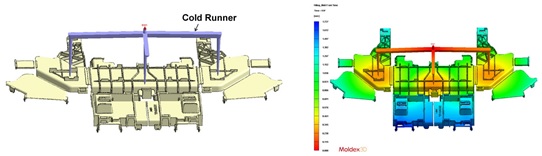
Fig. 4 Sistema di iniezione ottimale (canale freddo) e risultato del tempo di avanzamento della fusione
La Fig. 5 mostra gli schemi di riempimento con tre otturatori.
(Dati sui materiali: PP- SABIC PP PHC26 (MFI = 8g/10min)).
La Fig. 6 mostra gli schemi di riempimento con un sistema a canale freddo.
Questo progetto ha permesso alle tre porte di funzionare in modo molto simile con un sistema diretto a tre porte (dati del materiale: PP – TAIRIPROK4535 (MFI = 35 g/10 min)).
Di conseguenza, il team Stanley ha apportato una piccola modifica progettuale alla parte aggiungendo una nervatura vicino alla posizione del gate.
Questa nervatura ha permesso di riempire la parte più velocemente.
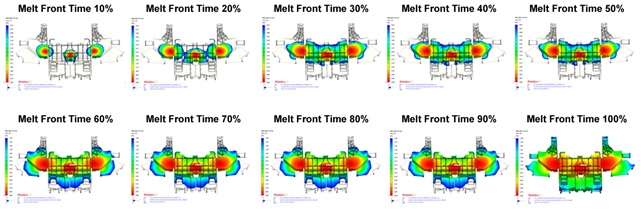
Fig. 5 I risultati della simulazione del tempo di front time (con otturatori)
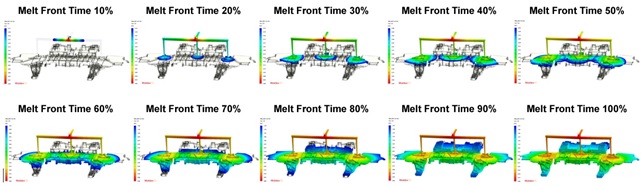
Fig. 6 I risultati della simulazione del tempo di front time (con un sistema a canale freddo)
Risultati
Le previsioni della simulazione con Moldex3D hanno aiutato STANLEY a raggiungere il sistema di iniezione ottimale senza problemi di riempimento e ottenere la deformazione minima con il sistema a canale freddo, eliminando la necessità di costose messa a punto o rilavorazione degli utensili.
Infine, STANLEY è stata in grado di completare il progetto in tempo per soddisfare le aspettative di time-to-market con il cliente.