PEGATRON con Moldex3D ha migliorato la copertura custodia di base del tablet del 92%
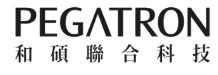
Profilo del cliente
Cliente: PEGATRON Corporation
Nazione: Taiwan
Settore: Elettronica
PEGATRON Corporation è stata fondata nel 2008. Con un’importante esperienza di sviluppo del prodotto e
di produzione integrata verticalmente, si impegnano a fornire ai clienti un design innovativo, una
produzione sistematica e un servizio di produzione di altissimo livello.
PEGATRON ha unito le industrie EMS e ODM per diventare un'azienda emergente di Design and
Manufacturing Service (DMS). (Fonte: http://
www.PEGATRONcorp.com)
Premessa
Al fine di creare parti più leggere e sottili, gli ingegneri PEGATRON sono stati incaricati di ridurre lo spessore
del coperchio di una custodia di base inferiore da 1,5 mm a 1 mm e aggiungere una parte di inserto
metallico di rinforzo, 0,5 mm di spessore, al design originale (Fig. 1).
Lo stampaggio di parti a pareti sottili è solitamente molto impegnativo e creare molti problemi come
squilibri, torsioni, planarità, deformazione e l'integrità strutturale meccanica. Gli ingegneri PEGATRON
hanno utilizzato il software di simulazione Moldex3D per ottimizzare i progetti degli stampi, ridurre il ritiro
e le deformazioni e convalidare la resistenza della parte attraverso l'integrazione con l'analisi FEA.
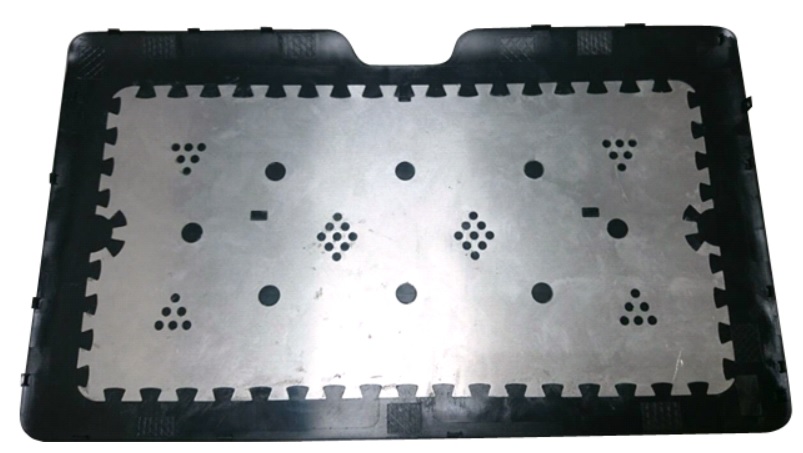
Fig. 1 Questa parte con inserto metallico e parete sottile
Sfide
· Mancato o non completo riempimento nelle pareti sottili
· Linee di saldatura critiche e Trappole d'aria
· Esitazioni e Restringimento causato da diverso spessore della parete
Soluzioni
Con Moldex3D, gli ingegneri di PEGATRON sono stati in grado di analizzare le cause della deformazione,
riducendo con successo lo spostamento di z del 92% e assicurando che i requisiti di resistenza dei
componenti fossero soddisfatti con l'integrazione di analisi strutturale fatta con ANSYS.
Benefici
· Spessore della parte metallica, obiettivo di 1 mm, riducendo lo spessore del 23%
· La deformazione totale significativamente del 92%
· Riduzione della perdita di pressione dell'8,3%
· Scarti ridotti del 13%
· Risparmiato oltre il 6% dei costi di produzione con l’utilizzo di inseti nello stampo
Caso di studio
Nel processo di stampaggio delle parti elettriche, il raffreddamento è un fattore chiave delle prestazioni
finali del prodotto.
È comune usare ventilatori per la dissipazione di calore, ma in alcuni casi senza ventola, possiamo utilizzare
solo un pad termico in alluminio o rame come inserto metallico nella cavità/parte.
Più spessa e più ampia è la piastra metallica, migliore sarà l'efficienza di raffreddamento.
L'altezza z del prodotto, in questo caso, è fissata a causa delle specifiche di progetto e marketing.
Pertanto, se lo spessore della piastra metallica è aumentato, lo spessore della parte deve essere diminuito.
Inoltre, la struttura deve essere abbastanza forte per soddisfare le specifiche meccaniche e di resistenza del
prodotto.
PEGATRON ha effettuato prove termiche attraverso il loro stampo esistente con un inserto metallico e
identificato migliori possibilità di risultato in termini di dissipazione.
Pertanto, hanno deciso di modificare lo stampo originale e il design della parte (Fig. 2).
Dopo di che, hanno cercato di migliorare il processo di produzione, la qualità del prodotto, e la resistenza
della struttura attraverso 3 fasi.
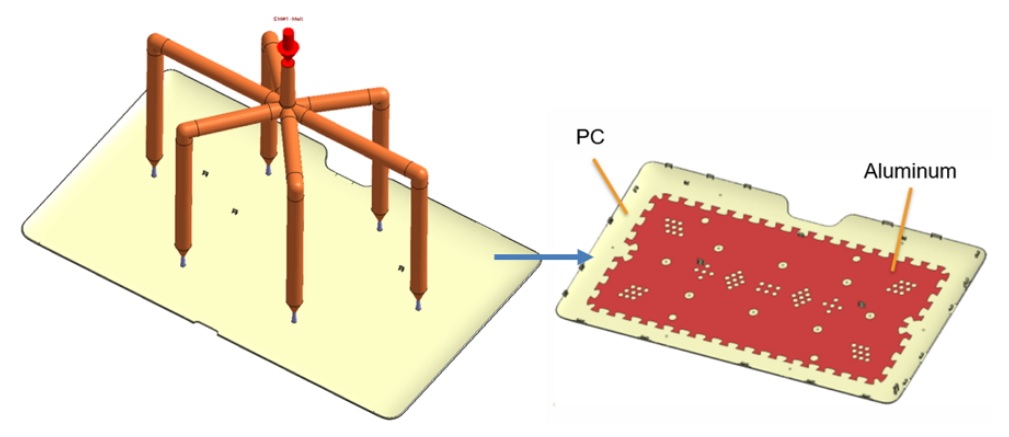
Fig. 2 Disegni di parti originali (a sinistra) e modificati (a destra)
Attraverso il modulo di iniezione Moldex3D, PEGATRON ha scoperto che la pressione di abete rosso
avrebbe ottenuto fino a 135 Mpa a causa della parte sottile.
Così, hanno preso in considerazione di diminuire la lunghezza del runner e utilizzato Moldex3D per
convalidare i disegni originali e rivisti (Fig. 4).
Di conseguenza, hanno scoperto che la perdita di pressione era stata ridotta dell'8,3% e lo scarto era stato
ridotto del 13% nel caso 3. Pertanto, hanno deciso Case 3 come il design ottimizzato.
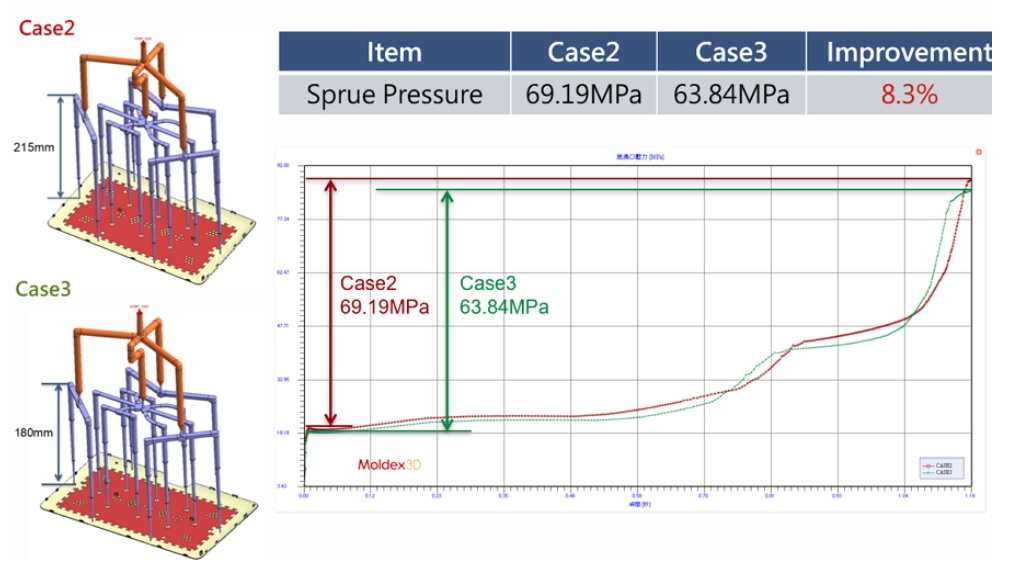
Fig. 4 Il confronto della pressione di diversi disegni di lunghezza del corridore
Successivamente, hanno cercato di migliorare la deformazione.
Moldex3D ha mostrato che la più deformazione maggiore nella direzione z era di 8,12 mm, che era oltre la
specifica 1.0mm.
Inoltre, il risultato della simulazione della deformazione ha indicato che l'impatto dell'effetto di ritiro era
maggiore di quello dovuto all'effetto termico (Fig. 5).
Per risolvere questo problema, PEGATRON ha tentato di aggiungere diverse percentuali di materiali di
contenuto in fibra di vetro nel prodotto e utilizzare Moldex3D per convalidare i risultati.
Hanno scoperto che si poteva ridurre efficacemente la deformazione per soddisfare le specifiche (Fig. 6).
La ragione era che la fibra si sarebbe orientata lungo la direzione di riempimento (asse X) per resistere al
restringimento.
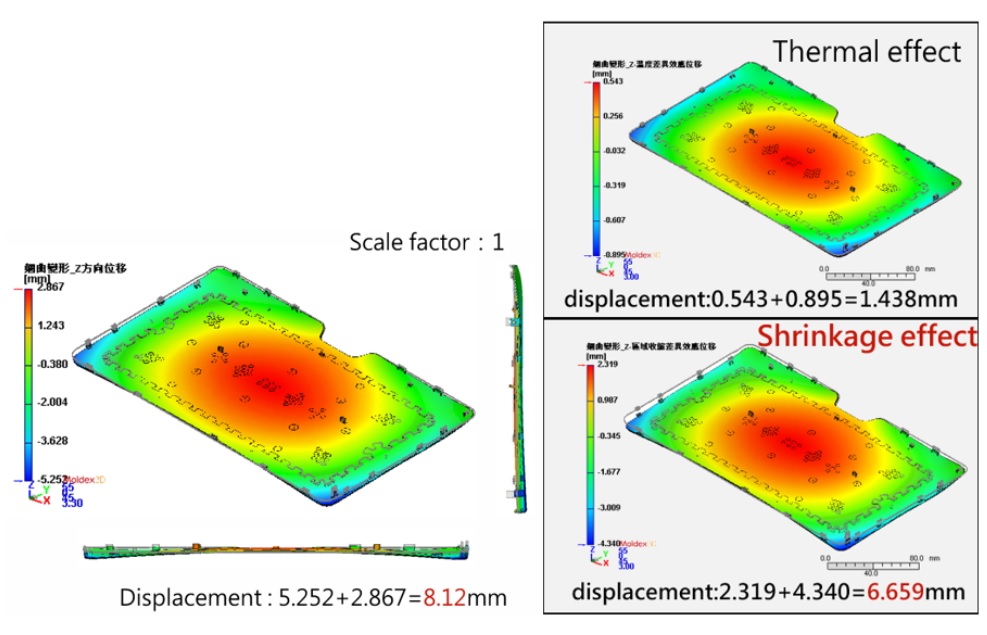
Fig. 5 I risultati della deformazione del materiale originale
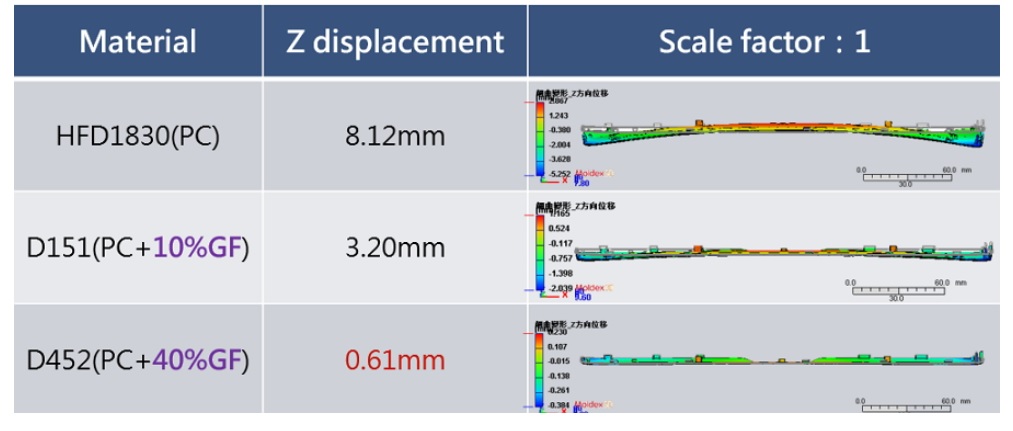
Fig. 6 Il confronto di spostamento tra i materiali con diverse percentuali di riempimento di fibra.
Nell'ultima fase, PEGATRON ha verificato se la struttura del prodotto era abbastanza forte o meno.
Hanno utilizzato l'interfaccia Moldex3D FEA per un'ulteriore analisi della sollecitazione considerando i
fattori indotti dallo stampaggio.
Dopo aver eseguito l'analisi della pressione e della torsione, hanno trovato l'inserto della parte e i materiali
con fillers che potevano contribuire efficacemente a ridurre lo spostamento in entrambe le prove (Fig. 7).
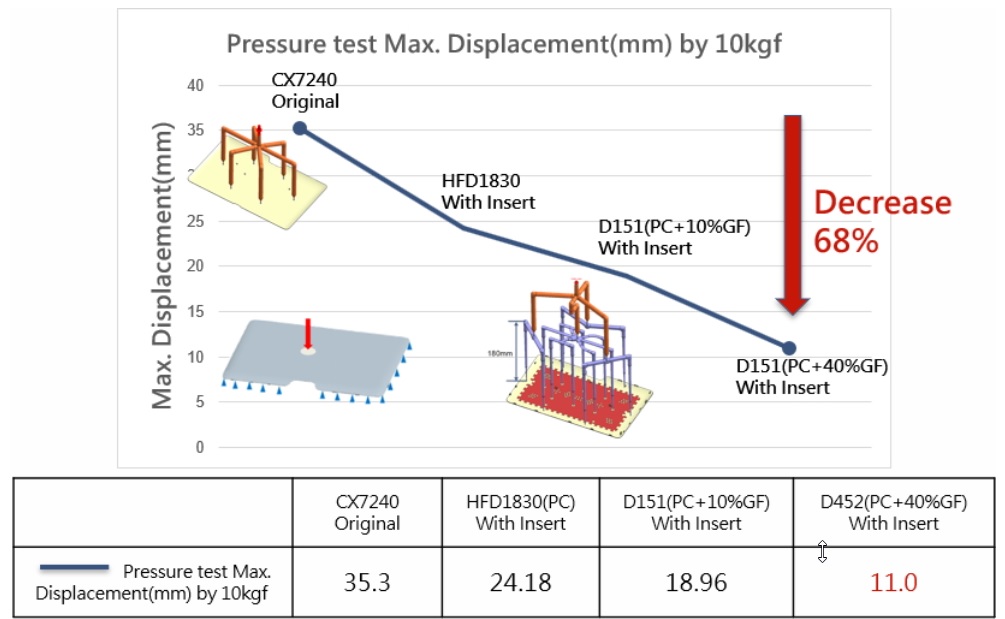
Fig. 7 I risultati dei test di pressione e torsione di diversi materiali e disegni di parti
Infine, PEGATRON ha verificato il risultato dell'analisi con l'esperimento e ha scoperto che i modelli di flusso
di simulazione e esperimento hanno le stesse tendenze.
Per quanto riguarda la verifica della planarità, i risultati dell'esperimento con materiali diversi erano tutti
coerenti con i risultati della simulazione (Fig. 8).
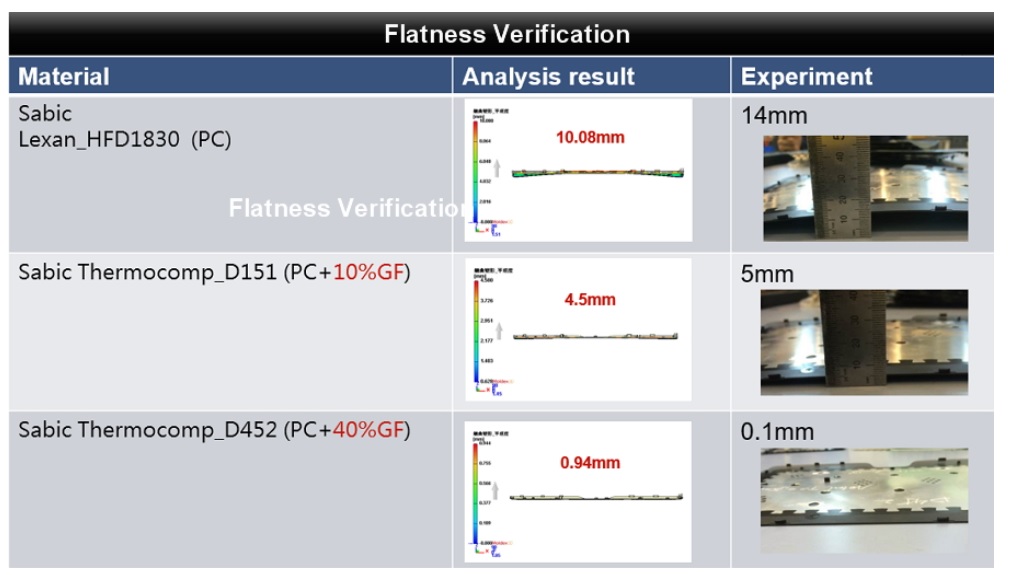
8 La verifica della planarità con i risultati dell'esperimento
Risultati
PEGATRON ha utilizzato il pacchetto Moldex3D Advanced per migliorare i progetti del prodotto e dello
stampo.
Attraverso l'analisi di Moldex3D, hanno anche trovato i principali fattori di deformazione e risolto questo
problema sostituendo diversi materiali e trovando la soluzione migliore.
Di conseguenza, il prodotto finale modellato ha soddisfatto con successo le specifiche per la resistenza
strutturale e la deformazione.
A cura di Lingo Shih, Engineer presso Product R&D Division, Moldex3D