Moldex3D consente l'ottimizzazione del design SABIC per l'estetica di superficie dei prodotti 2K-ICM
SABIC è leader globale in prodotti chimici diversificati, con sede in Arabia Saudita e India. Produce diversi tipi di prodotti tra cui prodotti chimici, materie prime e materie plastiche ad alte prestazioni, sostanze nutritive e metalli.
La premessa
Lo stampaggio a inietto-compressione a due colpi (2K-ICM) ha un immenso potenziale per realizzare soluzioni monocomponenti per componenti grandi e complessi con aree di elevata superficie, che attraverso un processo di iniezione standard richiederebbe un tonnellaggio pressa troppo elevato.

Lo sviluppo di difetti estetici come i segni di superficie in 2K-ICM è regolato da una complessa interazione di diversi fattori. Gli obiettivi erano dimostrare un framework di simulazione per 2K-ICM sfruttando Moldex3D per catturare gli aspetti chiave del processo per una geometria a nervature del modello e studiare i fattori geometrici e di elaborazione alla base dello sviluppo dei segni di caduta. Una simulazione completamente convalidata ha consentito l'adozione rapida di questa tecnologia minimizzando o eliminando il processo di try&error associato alla selezione della macchina e della qualità, alla progettazione dello stampo e all'ottimizzazione dei parametri di lavorazione.
Le sfide
•Mancanza di piena comprensione di 2K-ICM
•Linee guida di progettazione e processo complicate per 2K-ICM
•Segni (flow marks, linee di giunzione, bolle ecc.)
Le soluzioni
Il modulo Moldex3D Multi-Component Molding (MCM) consente una contabilità senza soluzione di continuità della storia termica per il primo e il secondo scatto.
I benefici
•Sviluppo delle competenze aziendali nel complesso processo di stampaggio del secondo colpo 2K considerando la storia termica del primo colpo
•Minimizzato o eliminato l'approccio sperimentale e try&error
•Design della parte ottimizzato per una migliore producibilità
•Processo di stampaggio ottimizzato e riduzione costo degli utensili in fase di progettazione
•Consentita selezione corretta della macchina (machine-mode-simulation), time-to-market più rapido e valutazione della complessità della progettazione dei pezzi
•Riduzione del tempo di ciclo complessivo del prodotto
•Maggiore credibilità / fiducia nei risultati della simulazione e capacità di suggerire soluzioni migliori ai clienti
Argomento di studio
Ora la tendenza chiave è la sostituzione di SMC (composto per stampaggio di lastre termoindurenti) con soluzioni termoplastiche per parti più grandi come pannelli di carrozzeria, deflettori dell'aria laterali di camion, tetto apribile panoramico, ecc. Ciò perché questa soluzione presenta molti vantaggi rispetto al processo SMC Sheet Molding Compression (come una maggiore flessibilità di progettazione, leggerezza, integrazione funzionale di due o più parti, ecc.)
La tecnologia 2K-ICM sta avendo una rapida crescita nel settore automotive e T&M, ma manca di metodologie di simulazione, in particolare sull'ottimizzazione dei processi per ottenere le proprietà finali desiderate. Raghavendra Janiwarad, ingegnere di ricerca presso SABIC, spiega la metodologia di simulazione 2K-ICM con Moldex3D per consentire l'ottimizzazione del design per l'estetica delle superfici.
L'obiettivo principale è catturare l'estetica, la deformazione e la distribuzione della temperatura della parte 2K-ICM (Fig. 1).
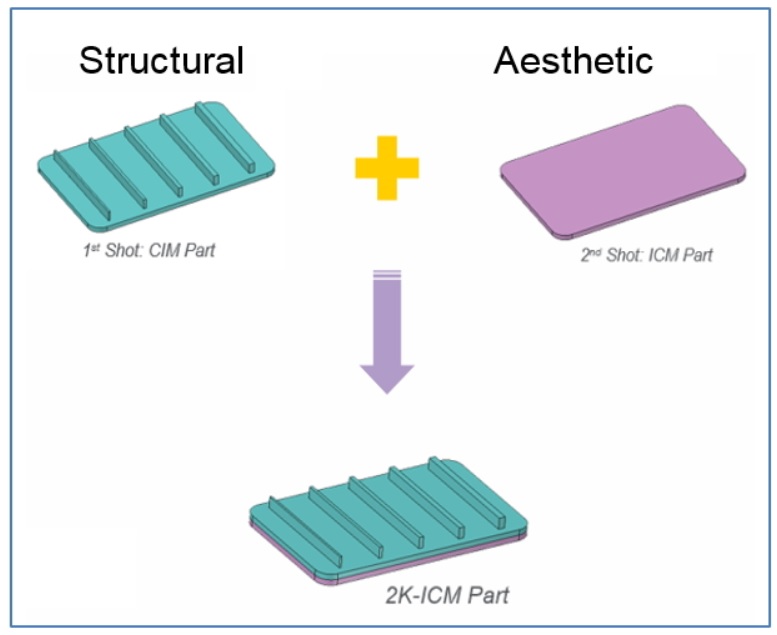
Fig. 1 La parte 2K-ICM in questo caso
Per la parte nervata (con spessori delle costole variabili) nel primo colpo, SABIC vorrebbe sondare le dimensioni delle nervature e gli effetti termici sulla superficie estetica del secondo colpo.
Il processo di analisi è mostrato in Fig. 2.
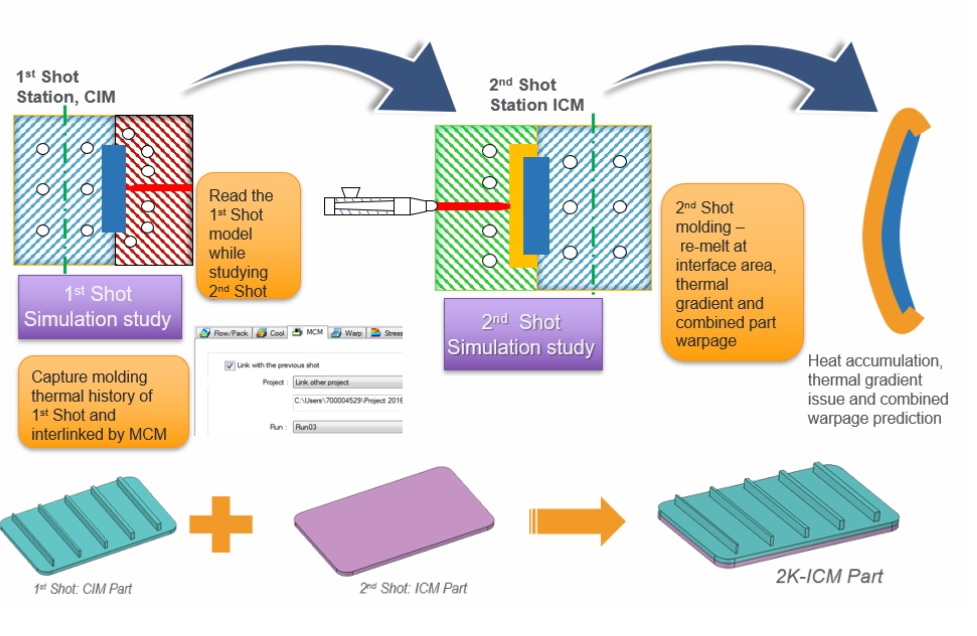
Fig. 2 Il processo di analisi
Secondo i risultati della simulazione di Moldex3D del primo colpo (CIM), il segno del risucchio è diventato progressivamente più prominente con l'aumentare dello spessore delle costole (Fig. 3). Il team SABIC ha anche confermato che più spesse erano le costole, maggiore era la massa termica. Ciò comporterebbe inoltre un gradiente termico più ripido e una maggiore variazione XYZ del ritiro volumetrico (Fig. 4).
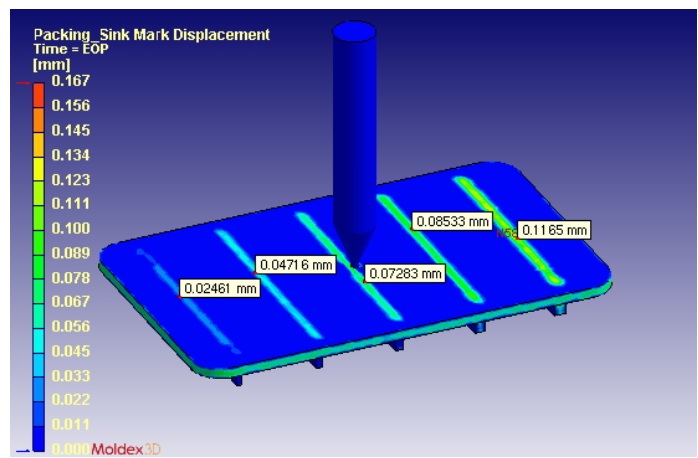
Fig. 3 I risultati della simulazione del segno del risucchio del primo colpo
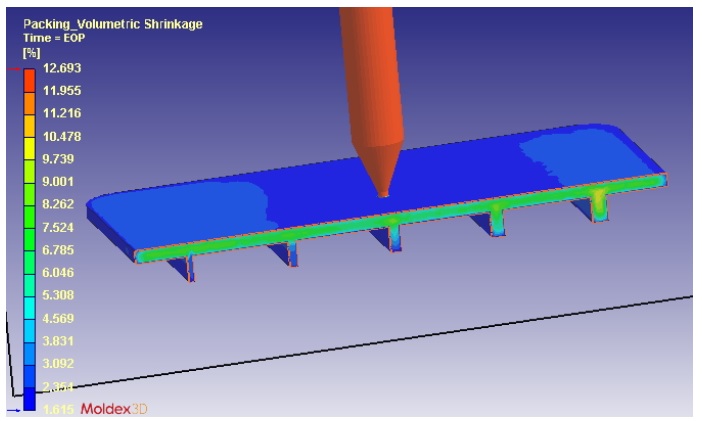
Fig. 4 Il risultato dell'analisi di contrazione volumetrica
Successivamente, SABIC ha provato a simulare il transitorio di temperatura nel secondo colpo (ICM).
La cronologia della temperatura del primo colpo viene catturata nella simulazione del secondo colpo Moldex3D (Fig. 5). Il risultato della simulazione del secondo colpo fornisce approfondimenti dettagliati sull'evoluzione della temperatura nell'interfaccia tra i due colpi (Fig. 6).
La temperatura nel primo colpo all'interfaccia si avvicina a 170 ° C, indicando la fusione del PC dal primo colpo - tali dettagli non sono facilmente osservabili con misurazioni sperimentali.
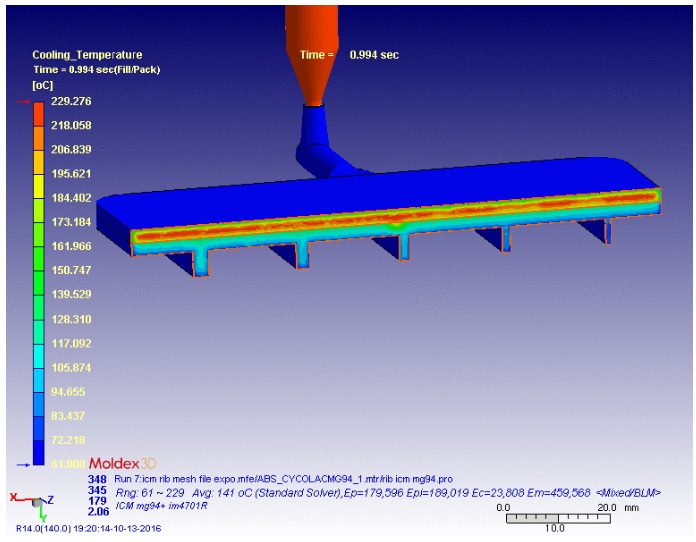
Fig. 5 I risultati della temperatura del secondo colpo in Moldex3D
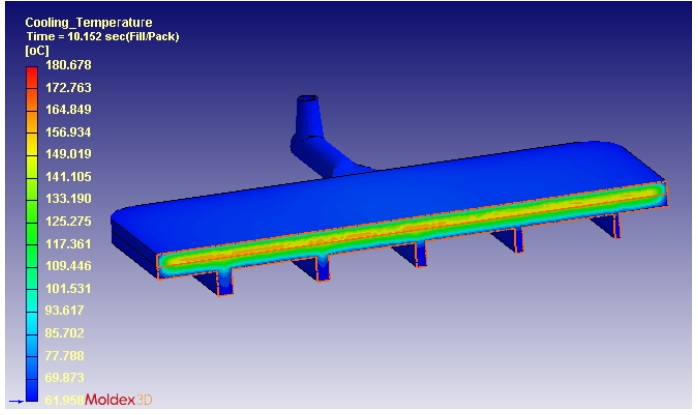
Fig. 6 Il risultato della simulazione del secondo scatto fornisce approfondimenti dettagliati sull'evoluzione della temperatura nell'interfaccia tra i due colpi.
Il trasferimento di calore dalla fusione nel secondo colpo, combinato con la presenza di nervature, crea ulteriore massa termica nella sezione centrale del primo colpo (Punto 4 in Fig. 7) e nell'interfaccia tra i due colpi (Punto 3, dove si osserva la rifusione (remelting)).
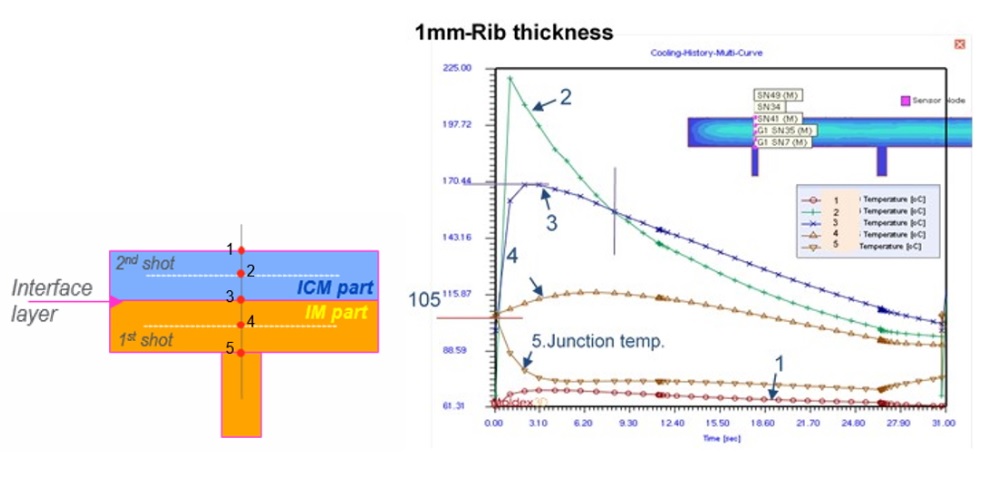
Fig. 7 L'evoluzione della temperatura della parte a due colpi
I risultati
Tramite Moldex3D, la storia termica dettagliata del primo colpo si collega perfettamente al secondo colpo. Le simulazioni del modulo Moldex3D MCM offrono approfondimenti su fenomeni sottili in 2K-ICM che potrebbero non essere valutati sperimentalmente. Questi includono i dettagli relativi all'interfaccia tra i due colpi, come la ri-fusione (remelting) localizzata nella regione del primo colpo e le caratteristiche geometriche che possono influire sulle proprietà estetiche e sulla deformazione delle parti. Tali simulazioni possono essere utili per l'ottimizzazione del processo associata alle applicazioni 2K-ICM per ridurre o eliminare la deformazione delle parti e i difetti di superficie (segni di superficie, risucchi ecc.).
Moldex3D Italia – Giorgio Nava – prt_2020_072