TomTom ha risolto un problema di forte deformazione in una parte del sistema di navigazione attraverso Moldex3D
Premessa
Il prodotto in questo caso è un coperchio anteriore della culla di un sistema di navigazione GPS per veicoli.
La deformazione è un problema significativo che deve essere controllato in modo da conformarsi alle esigenze estetiche e di montaggio, nonché il rispetto dele tolleranze di progetto. Nel progetto originale, la grandezza massima della deformazione risultava raggiungere 2,3 millimetri mentre il valore richiesto dalla qualità avrebbe dovuto essere meno di 0.3mm.
TomTom ha utilizzato Moldex3D per valutare diversi settaggi evitando diverse e costose prove fisiche, prevedendo ogni risultato di deformazione al variare degli scenari di progetto e di processo.
Come risultato, sono stati in grado di ottenere il design più efficace e soddisfare le specifiche richieste dalla qualità.
Le sfide
• Le prove di stampo mostrano un grave problema di deformazione.
• I valori di deformazione superano la specifica richiesta. (≥0.3mm)
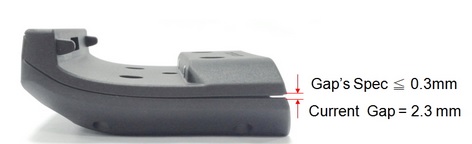
Fig.1 La deformazione rilevata sul pezzo stampato mostra una deformazione superiore ai 2,3 mm., ben oltre le specifcihe di progetto iniziali
Possibili soluzioni
TomTom ha utilizzato Moldex3D eDesign per simulare la temperatura, la caduta di pressione e le prospettive meccaniche di diversi progetti, via via in fase di miglioramento.
E’ stato così possibile individuare il progetto migliore
(Ottimizzazione del progetto).
Benefici
• Il divario di assemblaggio è stato notevolmente ridotto da 2,3 millimetri a 0,25 millimetri (rientrando nelle tolleranze richieste)
• Riduzione delle fase di prova fisica dello stampo a 3 volte
• Il tasso di rendimento in fase di produzione è passato dal 55% al 92%
• Riduzione dei costi di oltre $ 20.000
• Tempi di sviluppo ridotti a 6 settimane.
Il caso di studio
Il prodotto in questo caso è la copertina di una culla, e la sua funzione principale è quella di dare sostegno al dispositivo di navigazione.
L'obiettivo principale di questo caso è quello di ridurre una grave deformazione dopo lo stampaggio.
TomTom ha utilizzato
Moldex3D eDesign per simulare lo scenario di stampaggio del progetto originale e ha osservato da subito una serie evidente di problemi.
Nel progetto originale, il coperchio frontale è bloccato con la parte di accoppiamento e c'è un divario 2,3 millimetri che supera di pareccchio le specifiche che erano di 0,3 millimetri.
La Fig.2 mostra il modello CAD e il suo risultato, in cui si può osservare una grave deformazione al bordo della parte.
La linea tratteggiata in Fig. 2 mostra la tendenza della deformata.
La problematica interessa, in particolare la fase di assemblaggio. causando difetti di forma che avrebbero un impatto negativo diretto sulla funzionalità dimensionale dell’oggeto e il suo aspetto fisico.
Pertanto, al fine di risolvere questo problema e produrre prodotti di alta qualità con ottime caratteristiche estetici, ha portato TomTom a considerare diverse varianti e alternative
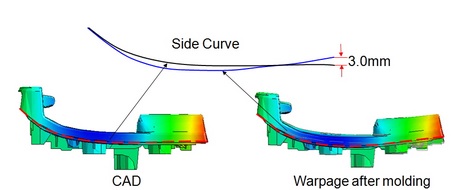
La Figura. 3 mostra una grande caduta di pressione che costituisce un fattore critico e contribuisce quantitativamente alla deflessione.
Così, lo studio si concentra principalmente su come ridurre questo calo di pressione.
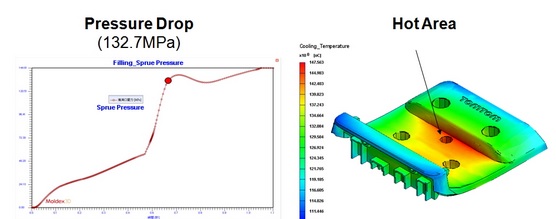
A parte la caduta di pressione, anche la distribuzione del calore non uniforme è un altro fattore che contribuisce alla deformazione totale e quindi anche questo contributo verrà considerato nella revisione del progetto.
TomTom ha considerato questi fattori influenti contemporaneamente per ridurre la deformazione.
La tabella 1 mostra 6 modifiche/varianti di progettazione e la combinazione dei diversi fattori.
Le 6 modifiche di progetto
Contributi alla deformazione Revisioni di progetto Modifiche Obiettivi
Fattori termici A Aggiungere canali di raffreddamento nelle zone calde(gestione differenziata) Per aumentare l’efficienza del circuito di raffreddamento e ridurre drasticamente il differenziale di temperatura tra la superficie superiore e quella inferiore della cavità
Fattori meccanici B Aggiungere nervature nelle aree meccanicamente deboli Aumentare la resistenza nelle zone più soggette alla deformazione
Caduta di pressione C Modificare la posizione ed il numero di gates Per migliorare il bilanciamento del flusso, ridurre la caduta di pressione ed avere una distribuzione più uniforme dei valori
Caduta di pressione D Aumentare lo spessore di 0.3 mm Per aumentare l’effetto della post-compressione, aumentando l’efficacia dell’impaccamento e la pressione del fuso ottenendo un più uniforme ritiro volumetrico nel pezzo
Caduta di pressione E Ridurre la lunghezza dei runners La riduzione del percorso compiuto dal fuso aumenta l’efficienza in fase di impaccamento ed una migliore distribuzione delle densità del materiale nella cavità.
Caduta di pressione F Modifica da canali freddi a canali caldi Riduce la lunghezza che deve percorrere il fuso (vedi anche E).
Tabella 2 è la sintesi relativa a caduta di pressione, deformazione dell'originale e ogni progetto revisionato. Come mostrato nei risultati, tipo C, D, E e F hanno un contributo superiore sulla riduzione della deformazione.
Così, TomTom combinato queste 4 modifiche di per ottenere un risultato ottimizzato.
La Figura. 4 mostra il confronto del disegno ottimizzato con la pressione più bassa, 31,25 MPa, e la deviazione minima con il modello CAD.
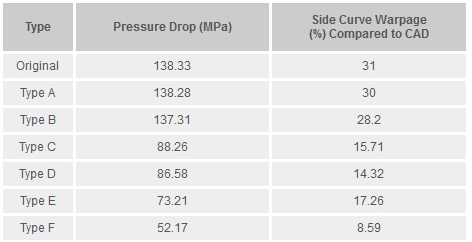
Tabella 2 Sintesi tra caduta di pressione e lo stato della deformazione
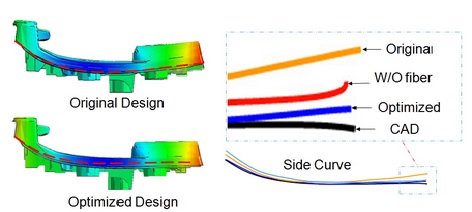
Figura. 4 Profilo ottimizzato relativo al diagramma di deflessione
Dopo la modifica del progetto, TomTom ha utilizzato Moldex3D eDesign per simulare sia il progetto originale sia il progetto ottimizzato.
I risultati delle diverse analisi sul progetto originale del prodotto ha mostrato evidenti problemi di deformazione.
Nel progetto ottimizzato, il miglioramento sia della deformazione sia dello svergolamento è evidente. TomTom ha poi confrontato i risultati delle simulazioni con i risultati effettivi di prova fisica dello stampo e ha trovato una forte correlazione tra i due risultati. Il divario tra il progetto originale (2,3 mm.) e il progetto ottimizzato è stato ridotto a 0,25 millimetri, che è un grande miglioramento ed ha permesso di rientare nelle specifiche di progetto richieste.
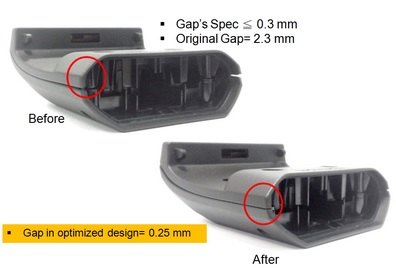
Figura. 11 La foto delle parti reali stampate con gap originale e gap ottimizzato
Riassumendo
Attraverso l'analisi di Moldex3D, TomTom è riuscita a comprendere nel migliore dei modi tendenze e valori di deformazione, essendo in grado di prevedere le potenziali difficoltà e difetti di stampaggio prima della produzione vera e propria.
Alla fine, TomTom ha potuto risolvere con successo problemi di produzione, ottimizzare sia il progetto del prodotto sia il progetto dello stampo.
TomTom è il principale fornitore al mondo di sistemi di localizzazione, e servizi focalizzati nel fornire di migliore esperienza di navigazione al mondo. Le soluzioni TomTom includono dispositivi portatili di navigazione, applicazioni per smart phone, orologi sportivi GPS, sistemi di infotainment, soluzioni di gestione della flotta, mappe e servizi in tempo reale, tra cui il pluripremiato TomTom HD Traffic.