Come combinare leggerezza e resistenza meccanica in una parte in plastica
Feng Chia University (FCU), Taiwan, in 50 anni, è costantemente aumentata in termini di dimensioni e capacità di creare nuovi laureati. Oltre 20.000 studenti sono attualmente iscritti a corsi di laurea, master e dottorato in ambiente ingegneristico
Premessa
Negli ultimi anni, l'industria manifatturiera ha ridotto il consumo di materiali, l'uso di energia e accorciato i cicli di produzione a causa della crescente consapevolezza ambientale (Green Circle Economy).
Tuttavia, molte parti strutturali in plastica sono lavorate con CNC, il che richiede cicli di produzione più lunghi e costi più elevati, con conseguente spreco di materiale.
In questo progetto, gli studenti della Feng Chia University miravano ad esplorare la possibilità di sostituire la lavorazione CNC con stampaggio a iniezione per creare dispositivi FRP nylon e vetro (PA66 +GF30%) per fornire parti leggere, funzionali e resistenti.
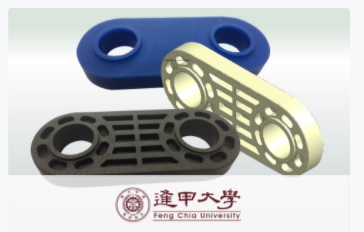
Sfide
•Per rinforzare le proprietà meccaniche della parte
•Per ridurre il ritiro e la deformazione delle parti
•Per contenere l’ovalizzazione in alcune zone del componente
Soluzioni
Gli studenti della Feng Chia University hanno utilizzato il software di simulazione Moldex3D per prevedere gli effetti delle fibre rinforzate e delle proprietà meccaniche dei materiali.
Inoltre, hanno anche utilizzato Moldex3D per esaminare l’ovalizzazione dei fori, lo spostamento degli assi (centrini) e convalidare i risultati con dati sperimentali.
I dati sperimentali hanno mostrato un buon accordo con i risultati della simulazione, confermando le capacità di predizione dell’analisi e simulazione con Moldex3D.
Con l'aiuto della simulazione e della convalida sperimentale, il ritiro, e la deformazione della parte, è stato ridotto con successo e ha soddisfatto le esigenze di rigidità e leggerezza richieste dal progetto.
Benefici
•Riduzione del ritiro del 22%
•Raggiunto l'obiettivo di leggerezza, riducendo il peso del 12%
•Raggiunta la resistenza strutturale richiesta
Caso di studio
In una macchina per lo stampaggio a soffiaggio, i blocchi di scorrimento sono parti importanti che collegano i cuscinetti a scorrimento e la preforma (Fig. 1).
Per ridurre i costi di produzione e raggiungere lo scopo della leggerezza, in questo studio, il team della Feng Chia University ha progettato di sostituire la lavorazione CNC con lo stampaggio a iniezione di plastica e prevedere il comportamento del flusso, l'orientamento della fibra, il restringimento, ecc. per il nuovo design del prodotto attraverso Moldex3D.
Il nuovo concetto di design del prodotto è illustrato nella fig. 2.
Fig. 1 I blocchi di scorrimento
Fig. 2 revisione del progetto (a: Disegno 2D; b: Modello 3D)
Per comprendere i problemi che possono verificarsi durante lo stampaggio del prodotto, il team ha confrontato l'esperimento fisico sul modello di test con l'analisi di Moldex3D, quindi ha applicato i risultati della ricerca allo sviluppo e alla produzione effettivi del prodotto.
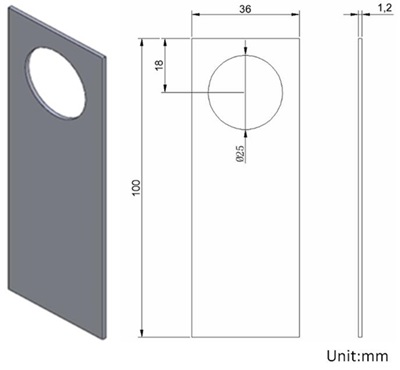
Fig. 3 Il modello di prova
La Fig. 3 mostra le dimensioni del modello di prova.
La rotondità del foro sulla parte era fondamentale poiché avrebbe dovuto collegare i cuscinetti di scorrimento.
Il progetto del sistema di iniezione includeva due formulazioni con gates vicini e lontani dal foro (Fig. 4).
È stato quindi osservato come le posizioni del punto di iniezione influenzano la rotondità del foro e le variazioni di ritiro del materiale.
Fig. 4 Posizionamenti diversi dei gates
Per confermare se la resistenza strutturale del prodotto soddisfacesse o meno l'obiettivo, il team ha utilizzato Moldex3D per prevedere il ritiro volumetrico e lineare, e l’ovalizzazione del prodotto dopo l'aggiunta della fibra.
E infine, i dati sperimentali hanno mostrato un buon accordo con i risultati della simulazione (come mostrato in Fig. 5).
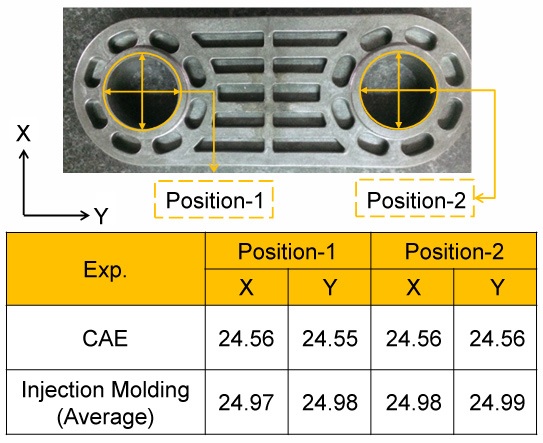
Fig. 5 Confronto tra i dati della simulazione Moldex3D e i dati sperimentali
Risultati
Grazie all'aiuto di Moldex3D, il team della Feng Chia University ha ridotto il peso del prodotto di oltre il 12% ottenendo una parte nei termini di leggerezza richiesti leggero (come mostrato in Fig. 6).
Hanno anche scoperto che il rinforzo della fibra di vetro poteva far sì che la struttura del prodotto raggiungesse la resistenza meccanica richiesta.
Il ritiro volumetrico del prodotto è stato migliorato di oltre il 22%, garantendo la rotondità richiesta.
Fig. 6 Confronto del peso tra il prodotto inizia e quello finale ottimizzato