Indagine sullo scorrimento di un materiale termoreattivo in fase di riempimento
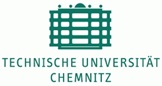
La Chemnitz University of Technology fu fondata nel 1836 come Royal Gewerbschule Chemnitz (Royal Mercantile College) a Chemnitz, in Germania. Rinominata nel 1963, la Chemnitz University of Technology è attualmente la terza università più grande della Sassonia con oltre 10.000 studenti iscritti. (Fonte: www.tu-chemnitz.de)
Sintesi
Il comportamento del flusso dei materiali e l’effetto di stabilizzazione del materiale nel processo di stampaggio a iniezione è una problematica particolarmente complessa che richiede continui approfondimenti. Pertanto, l'esistenza del fenomeno dello slittamento (Slip Effect) del materiale fuso nel contatto con la parete dello stampo è determinata da diversi fattori.
La problematica amplifica la sua complessità negli stampi 2K e 3K, dove le superfici di contatto non sono solo quelle dello stampo, ma si aggiungono quelle della prima (2K), e talvolta della seconda (3K).
L’utilizzo di materiali diversi e l’eventuale accoppiamento di materiali termoplastici con materiali reattivi complica ulteriormente il processo.
Questo “semplice” progetto dimostra come Moldex3D abbia aiutato uno laureando dell'Università di Tecnologia di Chemnitz a sviluppare un metodo utile per studiare il fenomeno dello slittamento del polimero sulla parete durante la fase di riempimento e come generare una scheda dati del materiale che può essere importata direttamente nel database dei materiali di Moldex3D per simulare il processo di stampaggio a iniezione di materiali termoindurenti con condizioni limite di slittamento sulla parete.
Sfide
•Per indagare il fenomeno dello slittamento (Slip Effect) sulla parete per materiali termoreattivi durante il riempimento
•Per creare una scheda dati del materiale per la simulazione dello stampaggio a iniezione con materiale termoreattivo
•Prevedere le curve master della cinetica reologica e curare i fenomeni cinetici a più velocità di riscaldamento
Soluzioni
In primo luogo, il gruppo di lavoro ha eseguito studi sperimentali di iniezione in diverse condizioni.
Si è scoperto che c'era un forte scivolamento sull'interfaccia tra il polimero (resina fenolica) e la superficie della parete dello stampo, che non era stato rilevato in maniera così consistente per lo stampaggio a iniezione con materiale termoplastico.
In secondo luogo, le proprietà reologiche e termiche dei composti di stampaggio a iniezione con materiale termoreattivo sono state misurate con molta precisione.
La risposta nel processo reale si è dimostrata molto coerente con i risultati della simulazione.
Successivamente, il gruppo di lavoro ha utilizzato il metodo numerico per creare una scheda tecnica del materiale e ha previsto le curve master della viscosità e curato la risposta cinetica a più velocità di scorrimento e conseguente riscaldamento (pre-curing). Infine, il team ha importato la scheda tecnica nel database dei materiali di Moldex3D per esaminare i risultati della simulazione del processo di stampaggio a iniezione considerando la condizione limite. I risultati sperimentali hanno mostrato che è stato trovato un forte effetto di slittamento nel contatto con la superficie della cavità.
Benefici
•Convalida dell'influenza del fenomeno dello slittamento sulla parete nello stampaggio a iniezione di materiale termoreattivo
•Confrontato il comportamento di flusso tra materiali termoreattivi e termoplastici
•Prodotto una Scheda Tecnica del Materiale per il processo di simulazione dello stampaggio a iniezione con materiale termoreattivo
Caso di studio
Il Dr. Tran-Ngoc Tu, Ricercatore presso la Chemnitz University of Technology, ha studiato i comportamenti di flusso del materiale Vyncolit X655 PF-(GF+Mineral) 80%) con condizioni di scivolamento e studiato sui fenomeni di interazione tra la superficie della parete anteriore di fusione e la parete della cavità durante il riempimento.
La Fig. 1 mostra il flusso instabile che si scioglie davanti alle plastiche termoset.
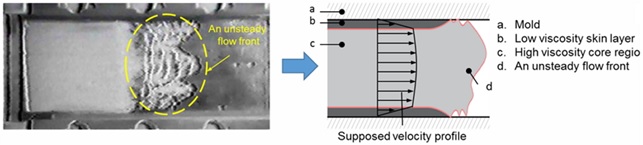
Fig. 1 Fronte di flusso instabile del polimero (resina fenolica) termoset (a sinistra) e presunto flusso caratteristico (a destra)
Per indagare i fenomeni di scivolamento, i ricercatori hanno “dipinto” manualmente per ottenere un segno nella cavità prima di ogni ciclo di iniezione.
Dopo essere stata espulsa dallo stampo, tramite analisi, la posizione del colore bianco è apparsa sulla superficie delle parti stampate, se la posizione del segno bianco mantiene la stessa posizione sulla superficie della cavità mostra che non si verifica alcuno slittamento dopo il completamento del ciclo di iniezione.
Al contrario, significa che c'è un evidente scivolamento sulla parete tra il polimero e la superficie della cavità. La fig. 2 mostra il metodo tecnico utilizzato: metodi di identificazione dei fenomeni di scivolamento.
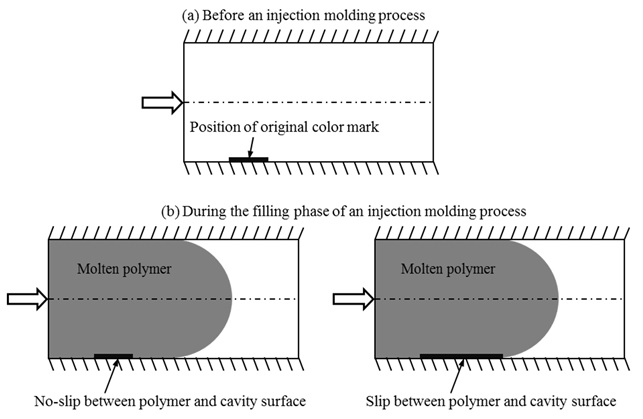
Fig. 2 Il metodo tecnico di identificazione dei fenomeni di scivolamento
I ricercatori hanno utilizzato una parte industriale complessa e a spirale per studiare i fenomeni di scivolamento, la posizione della linea di saldatura e la lunghezza del flusso.
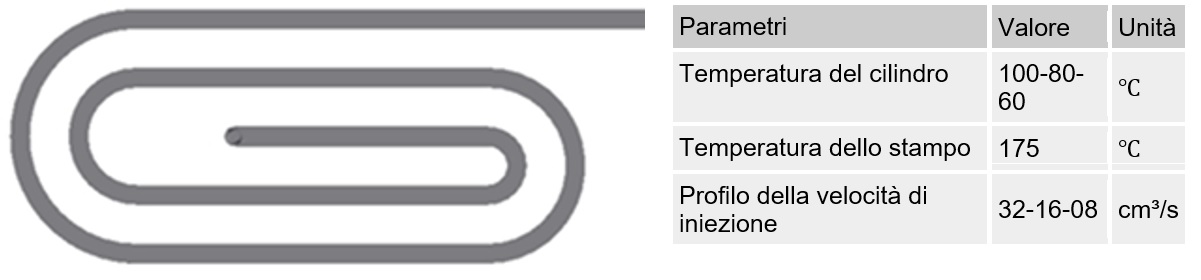
Fig. 3 mostra la direzione del flusso della parte a spirale con un singolo profilo di velocità di iniezione.
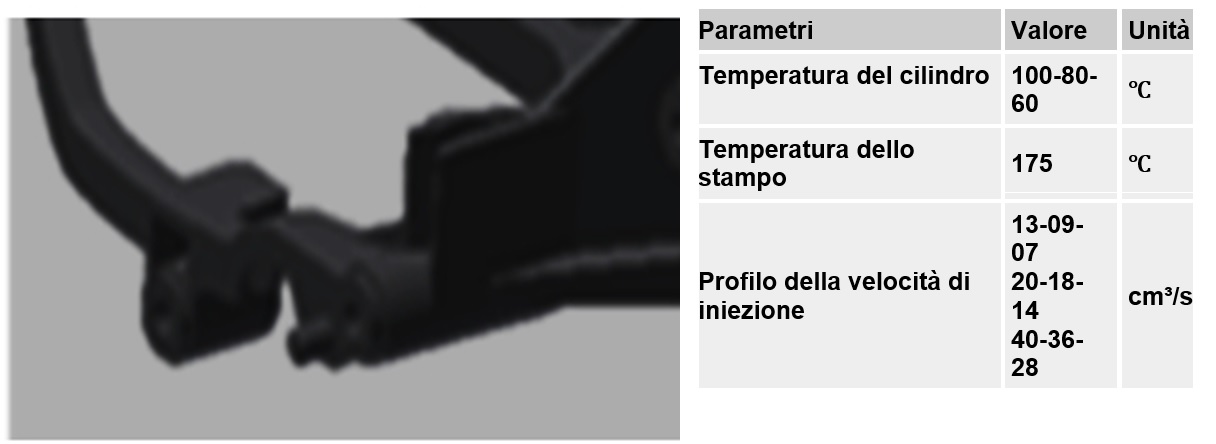
Fig. 4 mostra la parte industriale con il profilo di velocità e le tabelle 1 e 2 mostrano le condizioni di processo delle parti a spirale
I ricercatori hanno osservato nella spirale e nelle parti complesse, forti fenomeni di scivolamento che si verificano nella direzione del flusso tra la fusione fenolica e la superficie della cavità per tutte le condizioni di processo.
La traccia del “segno bianco” è stata osservata lungo la direzione del flusso di fusione nella superficie della parte.
La Fig. 5 mostra i forti fenomeni di scivolamento per entrambi i modelli.
Fig. 5 Scivolamento delle strisce bianche sulla superficie della cavità di una parte a spirale e complessa
Per prevedere la realtà nelle simulazioni numeriche, le proprietà del materiale sono uno dei fattori importanti per i calcoli numerici di stampaggio a iniezione.
In questo caso, i ricercatori hanno misurato le proprietà termiche utilizzando un calorimetro a scansione differenziale (DSC Q2000) e un misuratore di conducibilità termica (DTC 300) e misurato le proprietà reologiche del materiale utilizzando un reometro plate-plate (AR 2000).
I dati misurati degli strumenti sono stati utilizzati per sviluppare il modello numerico. La cinetica (Curing Kinetics) misurata a tre velocità di riscaldamento era di 5, 10 e 20 k/min.
E’ stato utilizzato il modello numerico Kamal (Curing Kinetics)) utilizzato per prevedere diverse velocità di riscaldamento per la velocità di reazione e il grado di curing è mostrato rispettivamente nella Fig. 6 e 7.
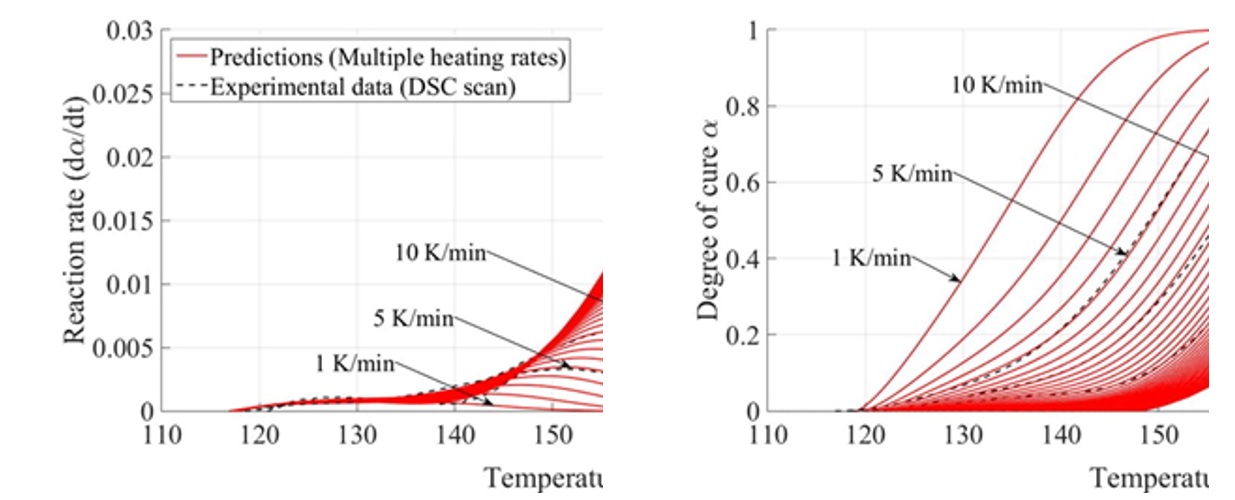
Fig. 6 Velocità di reazione Fig. 7 Grado di curing
Il modello Cross-Castro-Macosko è stato utilizzato per prevedere la viscosità del materiale con più velocità di riscaldamento. Le curve di viscosità previste hanno trovato un’ottima rispondenza con i dati sperimentali, come mostrato nelle fig. 8 e 9.
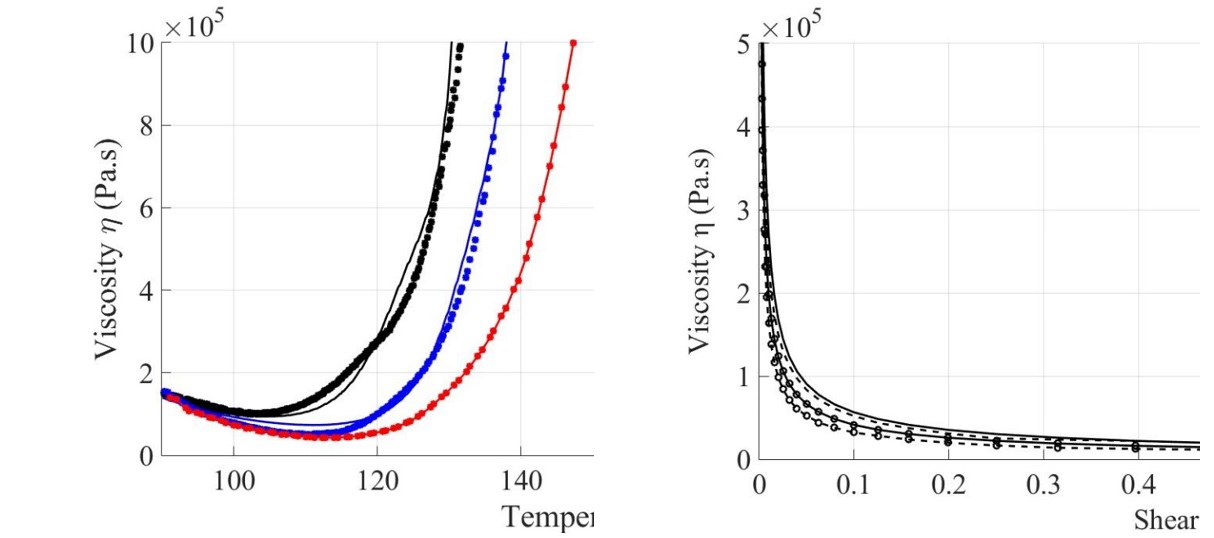
Fig. 8 Viscosità (temperatura) Fig. 9 Viscosità (velocità di taglio)
I ricercatori hanno convertito le proprietà del materiale previste nel formato dei dati del materiale con l'aiuto di Moldex3D.
Quindi, il file di dati del materiale è stato importato nel database Moldex3D Materiali per prevedere i risultati. I ricercatori hanno osservato che la lunghezza del flusso risultata dalla simulazione è Moldex3D e quella dell’esperimento reale hanno mostrato un’ottima corrispondenza (le condizioni di scivolamento per la parte a spirale).
Sono stati utilizzati diversi profili di velocità di iniezione nell'esperimento e nella simulazione per osservare il comportamento del modello di flusso e le possibili posizioni delle linee di saldatura (welding lines) e delle trappole d’aria. Moldex3D ha fornito diversi comportamenti in corrispondenza a diversi profili di velocità di iniezione. I ricercatori hanno potuto osservare le possibili posizioni delle linee di saldatura dalla parte incompiuta (esitazione nel flusso del materiale) (Fig. 10).
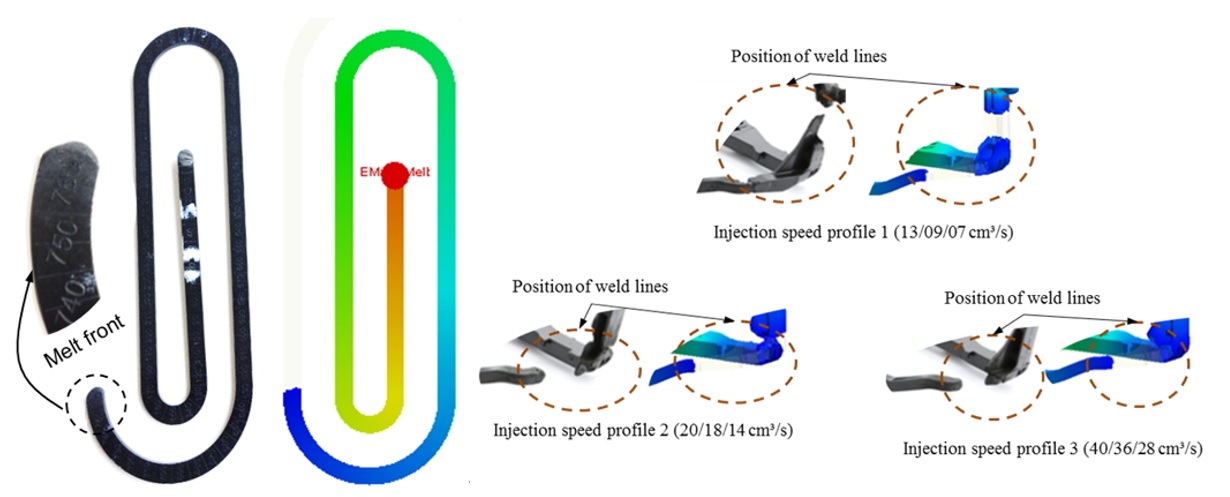
Fig. 10 Confronto tra le parti incomplete stampate a iniezione (a sinistra) e i corrispondenti modelli di riempimento previsti da Moldex3D (a destra)
I risultati dell'esperimento per la parte a spirale hanno mostrato chiaramente i diversi comportamenti del polimero nelle vicinanze del gate e via via sempre a distanza maggiore.
La previsione della simulazione a 43 secondi lo mostra intorno al 75% con una differenza contenuta del 4% inferiore rispetto ai dati dell'esperimento (79%) dalla figura 11. Dalla Fig. 12, i risultati della polimerizzazione mostrano che ci vogliono solo 50 secondi in più perché il polimero del nucleo fuso raggiunga il grado di stabilizzazione del 79%. Mostra che il file di materiale (MTX) utilizzato per il calcolo è consistente.
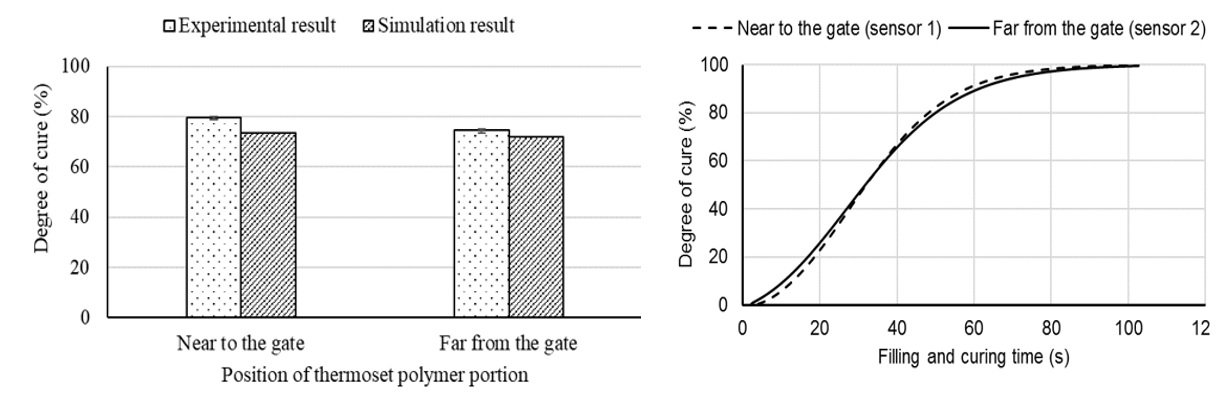
Fig. 11 Il confronto tra il grado di stabilizzazione sperimentale e simulato della parte a spirale
(il tempo di riempimento e polimerizzazione è di 43 s) Fig. 12 Il grado di cura del Vyncolit X655 fuso nella fase di riempimento e stabilizzazione prevista dalla simulazione
Risultati
Attraverso le analisi Moldex3D e l'esperimento, i ricercatori hanno osservato il forte comportamento di scivolamento tra la superficie della cavità e il fronte di fusione del polimero termoreattivo. I ricercatori hanno utilizzato Moldex3D per simulare il processo di polimerizzazione dello stampaggio a iniezione RIM, la lunghezza del flusso, la distribuzione della pressione, la viscosità, la linea di saldatura e altri parametri. Moldex3D mostra un buon accordo con i dati sperimentali.
Dopo aver considerato tutti i risultati, Moldex3D si è dimostrata una soluzione perfetta per prevedere lo scenario reale nello stampaggio a iniezione.
A cura di Yoganantham Natrayan, ingegnere del team di supporto tecnico, Moldex3D
MDXITA_ prt_2020_104