Il Cliente: Free-Free Industrial Corp. (Felli)
Paese: Taiwan
Settore: prodotti di consumo
Soluzione: Moldex3D Advanced Package; Flow, Pack, Cool, Designer BLM
Free-Free è leader mondiale nella produzione di articoli in acrilico, articoli per la tavola, tavoli, articoli da bagno, prodotti per ufficio, accessori 3C e prodotti per animali domestici. Free-Free è stata fondata nel 1985 dal presidente Mike Liu e dal direttore generale Sylvia Chang.
Free-Free Industrial Corp. è conosciuta a livello globale con il brand "Felli". (Fonte: http://www.felli.com.tw/about.php)
Agli ingegneri Felli fu assegnato il compito di produrre grandi quantità di un contenitore per alimenti. Gli obiettivi di sviluppo erano raggiungere tempi di ciclo più brevi, diremmo ottimali, al tempo stesso un prodotto di qualità elevata e ridurre la necessità di post-elaborazione.
Il sistema di alimentazione scelto era un sistema di canali caldi con controllo dell’apertura e chiusura del gate per ottimizzare l’utilizzo di materiale ed evitare difetti superficiali.
Tuttavia, l’effetto dovuto ai diversi gradienti di temperatura nello scorrimento del flusso nelle camere ha provocato uno sbilanciamento inaspettato e causato linee di saldatura, trappole d'aria e segni superficiali giudicati non accettabili dalla qualità.
I progettisti di Felli hanno utilizzato Moldex3D per eseguire una serie di analisi accurate per determinare la causa principale di questo effetto (chiamato corner effect) e convalidare, alla fine, la soluzione proposta, riuscendo finalmente ad ottenere una produzione costante e di alta qualità.
E’ stata utilizzata la tecnologia BLM (Boundary Layer Mesh) di Moldex3D per trovare le soluzioni allo squilibrio del flusso
Questo prodotto è un contenitore trasparente realizzato in AS, con dimensioni 140mm * 140mm * 210mm (Fig. 1).
Lo stampo è progettato come uno stampo a due cavità, che viene riempito dal fondo del serbatoio utilizzando un canale caldo con controllo in apertura e chiusura della valvola.
Il processo è stato pianificato per la produzione di massa (milioni di pezzi) e richiede produzione continua 24/7 senza interruzioni se non per manutenzione macchina.
Pertanto, come ottenere una produzione stabile e continua è stato il problema più importante.
Sebbene sia stato utilizzato un sistema di canali caldi con controllo e un eccellente design del canale di raffreddamento per migliorare i difetti della superficie e ridurre con successo i cicli di stampaggio, c'erano ancora da eliminare o ridurre l’impatto delle linee di saldatura, trappole d'aria e segni di flusso di calore e/o stress del materiale causati da uno squilibrio del flusso.

Fig.1 Il prodotto: serbatoio trasparente
Secondo la simulazione Moldex3D, c'era davvero un fenomeno di squilibrio del flusso (Fig. 2).
Osservando ulteriormente il profilo del risultato della temperatura, si può scoprire che la colla a caldo si diffonde all'esterno a causa dell'effetto angolo causato dalla fusione a caldo che esclude il perno della valvola e continua fino al prodotto finale (Fig. 3).
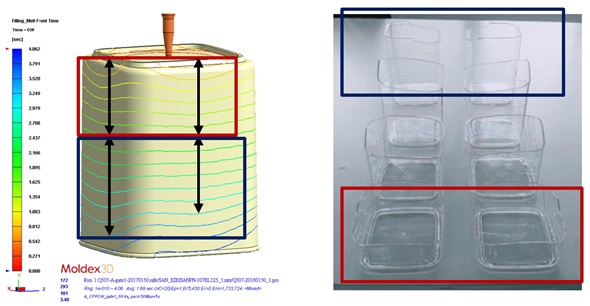
Fig. 2 Lo squilibrio di flusso indicato dai contorni frontali di fusione nella simulazione Moldxe3D (a sinistra) è coerente con i risultati sperimentali (a destra).
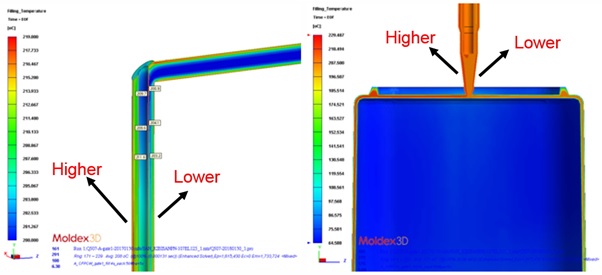
Fig. 3 Osservando il profilo della temperatura, si rileva che la distribuzione della temperatura avviene dopo che il fuso passa attraverso il perno della valvola (a sinistra) e continua al prodotto (a destra).
Secondo i risultati della simulazione e la verifica sperimentale, è chiaramente dimostrato che il perno della valvola è la chiave per influenzare il bilanciamento del flusso.
Pertanto, Felli ha provato a verificare rapidamente i risultati modificando la lunghezza del perno della valvola e/o rimuovendo il perno della valvola.
Attraverso la simulazione CAE, hanno scoperto che il bilanciamento del flusso è stato notevolmente migliorato dopo la rimozione del perno della valvola (Fig. 4).
La verifica effettiva corrisponde perfettamente ai risultati della simulazione (Fig. 5).
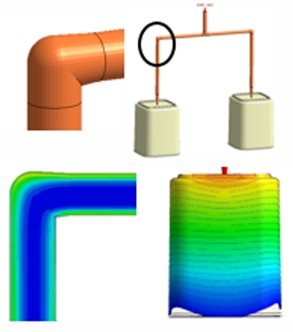
Fig. 4 Risultati della simulazione con il perno della valvola rimosso.
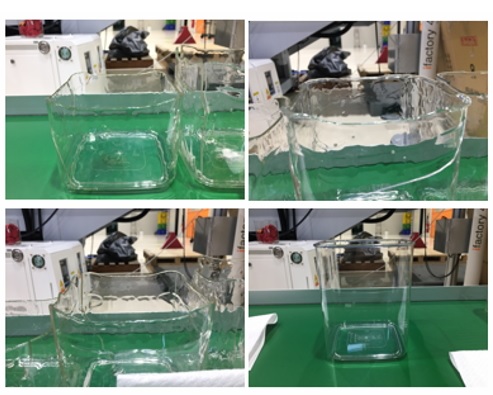
Fig. 5 La verifica sperimentale
Infine, Felli ha ottimizzato il design del sistema di alimentazione (runner) con la tecnologia “flipper” per ridurre la differenza di temperatura durante il percorso del fuso lungo i canali di alimentazione (Fig. 6) e ha ulteriormente migliorato l'equilibrio del flusso (Fig. 7).
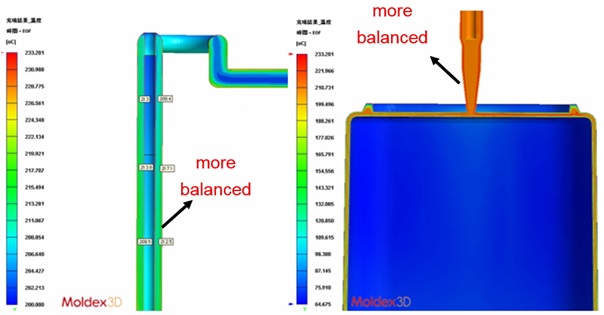
Fig. 6 Attraverso la tecnologia flipper, la differenza di temperatura dopo il passaggio alla valvola di controllo viene ridotta (a sinistra) e il bilanciamento del flusso viene migliorato (a destra).
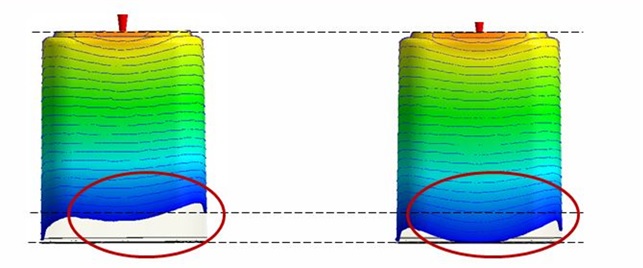
Fig. 7 Lo squilibrio di flusso è stato migliorato nel design ottimizzato (a destra)
Attraverso l'analisi di Moldex3D e le verifiche effettive, Felli ha scoperto la vera causa di questo problema e l’utilizzo di un sistema di simulazione come Moldex3D ha permesso una chiara indicazione per apportare i necessari miglioramenti al sistema di alimentazione a camere calde. Dopo la riconvalida, sempre tramite Moldex3D, il problema è stato risolto, ridotto il tasso di difetto dal 100% allo 0% e ridotto il tasso di difetto della produzione effettiva allo 0,05%, evitando l'implementazione di contromisure non efficienti, che andavano ad aumentare i costi di produzione.
I risultati
La tecnologia Moldex3D ha consentito ai progettisti di Felli di identificare in modo preciso gli squilibri di flusso e definire una distribuzione della temperatura accurata, raggiungendo il risultato. Inoltre, gli ingegneri Felli hanno utilizzato Moldex3D per studiare l'effetto dei componenti delle camere calde sul bilanciamento del flusso.
I risultati della simulazione si sono abbinati bene ai risultati sperimentali e hanno dimostrato che il perno della valvola è la chiave per migliorare gli squilibri di riempimento.
Con Moldex3D, Felli ha identificato con successo la causa principale dell'effetto dovuto al gradiente di temperatura nel percorso del fuso lungo i canali della camera calda e ha ottimizzato il design del runner per ridurre la differenza di temperatura quando il flusso di fusione supera il perno della valvola, migliorando lo squilibrio del flusso indotto da questo effetto (corner effect).