Un metodo per migliorare la qualità della superficie delle cornici dei fendinebbia per autoveicoli
A cura di Sam Hsieh, Manager presso il team di supporto tecnico, Moldex3D
Profilo del cliente
Cliente: TONG YANG GROUP
Paese: Taiwan
Settore: Automotive
Soluzione: Moldex3D Advanced Package
TONG YANG GROUP è stato fondato nel 1952. Oggi conta un totale di 25 stabilimenti di produzione e 9.307 dipendenti in tutto il mondo. I loro prodotti principali sono plastica, lamiera, gruppi di ventole di raffreddamento, sviluppo di utensili e prodotti per la verniciatura e la missione aziendale è fornire la migliore qualità di parti sia in ambiente automobilistico sia consumer.
Premessa
Gli ingegneri di Tong Yang sono stati incaricati di risolvere i difetti estetici in una parte stampata a iniezione di un fendinebbia in plastica (Fig. 1, 2).
Poiché si tratta di un componente esterno per autoveicoli, le linee di saldatura dovrebbero essere evitate ove possibile. Inoltre, le linee di saldatura non dovrebbero apparire nemmeno sulla superficie del componente di bloccaggio.
Gli ingegneri di Tong Yang hanno utilizzato Moldex3D per capire in che modo i layout delle guide possano influenzare la posizione e l'angolo delle linee di saldatura.
Inoltre, Moldex3D ha assistito Tong Yang nell'ottimizzazione dello spessore delle pareti per risolvere le trappole d'aria, affrontando con successo i problemi estetici nella parte del fendinebbia.
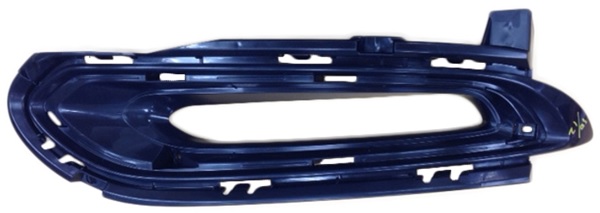
Fig. 1 La parte del fendinebbia in questo caso
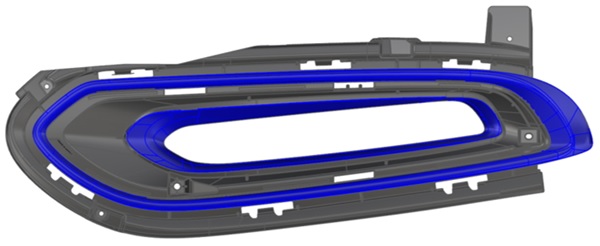
Fig. 2 Il colore blu indica le aree dell'aspetto visibile
Sfide
•Evitare che si formino linee di saldatura nelle aree dell'aspetto visibile
•Trovare un design rivisto efficace per risolvere il problema della trappola d'aria
Soluzioni
Moldex3D ha permesso agli ingegneri di Tony Yang di analizzare varie posizioni dei punti di iniezione per ottimizzare i modelli di riempimento ed evitare linee di saldatura sulla superficie del pezzo. Inoltre, sulla base dei risultati dell'analisi del flusso di Moldex3D, gli ingegneri di Tong Yang sono stati in grado di rilevare la trappola d'aria nel lato del nucleo e apportare le modifiche necessarie al progetto, inclusa la regolazione dello spessore della parete, per risolvere le trappole d'aria e migliorare le posizioni della linea di saldatura.
Benefici
•Difetti superficiali risolti, inclusi trappole d'aria e linee di saldatura
•Evitate costose rilavorazioni dello stampo
•Processo decisionale di progettazione accelerato
Argomento di studio
Lo sviluppo di questa parte del fendinebbia è stato suddiviso due fasi: prove di progettazione e stampo.
Le simulazioni Moldex3D vengono eseguite in entrambe le fasi di sviluppo per scopi diversi.
Durante la fase di progettazione prima di realizzare lo stampo, lo scopo principale era quello di verificare il progetto del sistema di alimentazione e prevedere i potenziali difetti estetici.
La verifica del progetto del gate considerava 3 tipi diversi da simulare che combinavano diverse quantità di gates, posizione e layout del runner.
Il criterio decisionale di progettazione riguardava l’entità dei difetti estetici provocati dalla linea di saldatura e dalle trappole d'aria (potenziali bruciature).
Il progetto che rivelava la minima difettosità è stato utilizzato per ulteriori lavori di ottimizzazione della parte estetica. Dopo che lo stampo è stato realizzato e la prima prova dello stampo è stata eseguita, i risultati della simulazione sono stati convalidati con la parte stampata effettiva. Inoltre, i difetti osservati dalla prova di stampo sono stati analizzati per cercare la causa principale e le soluzioni più efficaci (Fig. 3).
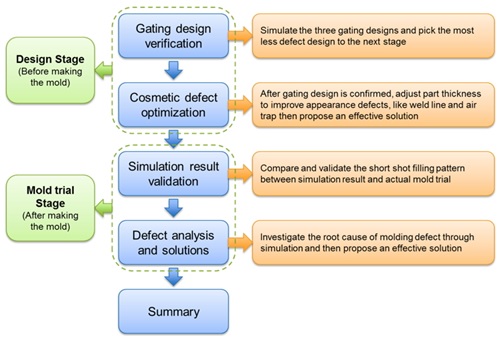
Fig. 3 Scopo principale nelle diverse fasi di sviluppo
La verifica del progetto del sistema di alimentazione è stata la prima attività a cui è stata indirizzata la simulazione con Moldex3D. Come mostrato in Fig. 4, il Tipo A ha un unico gate situato nella parte centrale inferiore della parte. Il numero di gates nel tipo di progetto B è lo stesso del tipo A, ma la posizione del gate è in basso a destra della parte.
L'ultimo progetto di tipo C ha due gates situate sui lati sinistro e destro. Dopo aver completato tutte le analisi dei progetti, le linee di saldatura e le trappole d'aria che si sono verificate sulle aree dell'aspetto visibile sono state analizzate per il processo decisionale finale di progettazione del sistema di alimentazione.
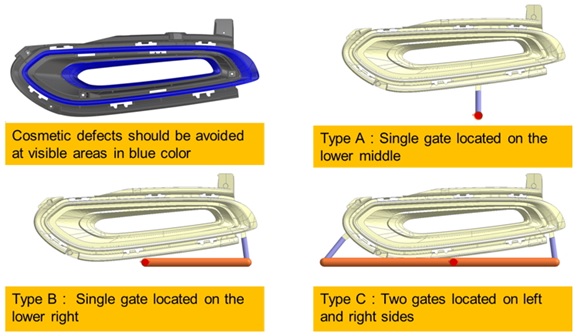
Fig. 4 Requisiti di qualità dell'aspetto e tre tipi di design del cancello
Secondo la tabella di confronto linea di saldatura/ trappola d'aria, dai risultati dell'analisi in Fig. 5, il Tipo B ha i difetti minimi, quindi è stato utilizzato per ulteriori lavori di ottimizzazione dei difetti estetici.
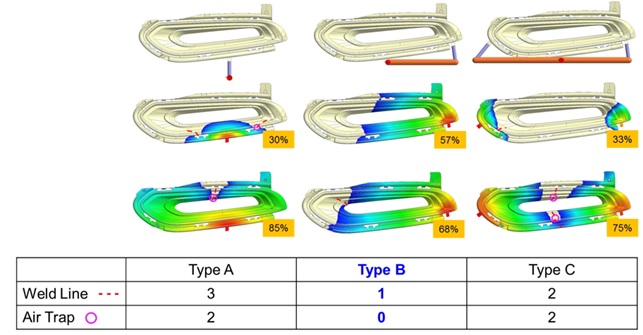
Fig. 5 Confronto delle previsioni tra 3 tipi di design del cancello
L'angolo di saldatura è uno degli indici comunemente utilizzati per confrontare e giudicare la qualità della linea di saldatura. L'angolo di saldatura nel design dello spessore della parte originale è di circa 120 gradi. Dopo l'ottimizzazione del progetto dello spessore della parte come mostrato in Fig. 6, l'angolo di saldatura è stato aumentato da 120 a 140 gradi, il che significa che la linea di saldatura è più corta e meno visibile.
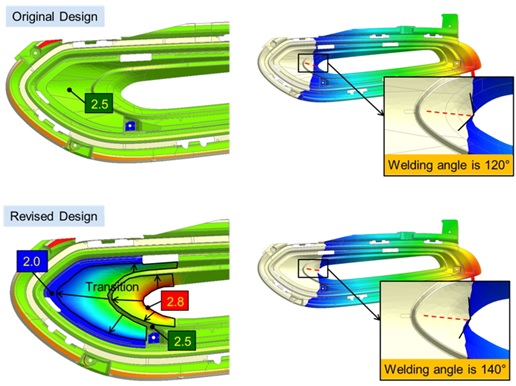
Fig.6 L'ottimizzazione dello spessore della parte per migliorare la qualità della linea di saldatura
Dopo che lo stampo è stato realizzato e la prima prova dello stampo è stata eseguita, i risultati della simulazione sono stati convalidati con una parte stampata. Come mostrato nelle immagini di confronto alle diverse percentuali di riempimento (Fig. 7), il risultato della simulazione era coerente con la parte effettiva.
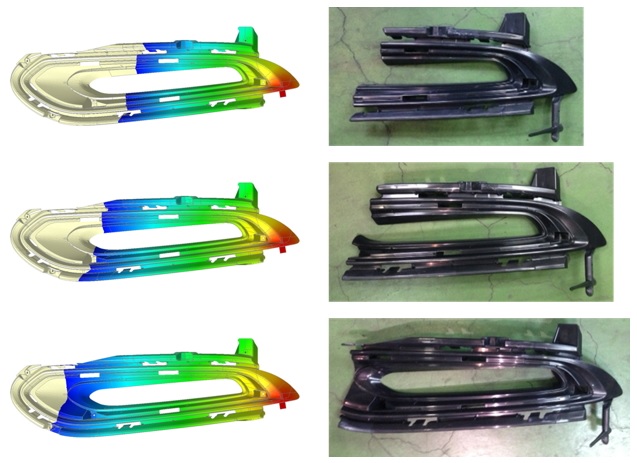
Fig.7 Confronto dei modelli di riempimento
Tuttavia, è stata osservata una trappola d'aria sulla superficie della parte nella prima prova di stampo.
La trappola d'aria si verifica in un'area visibile sul lato della cavità dello stampo dove non è consentito realizzare alcuna fessura di ventilazione.
Il fronte di fusione mostra lo stesso motivo di riempimento dove la regione d'angolo scorre più velocemente delle regioni circostanti.
La causa principale è la caratteristica geometrica del raccordo: lo spessore della parte diventa più spesso (3,5 mm) rispetto allo spessore principale (2,5 mm), quindi la regione più spessa scorre più velocemente poiché ha una resistenza inferiore.
La soluzione che prevede lo spessore della parte core-out nella regione di 3,5 mm è sta analizzata e verificata con la simulazione Moldex3D (Fig. 8).
In base al risultato con il modello core-out (Fig. 9), si verificano due linee di saldatura aggiuntive.
Tuttavia, le due linee di saldatura aggiuntive si trovano in regioni invisibili, in zona “non” estetica e quindi è accettabile.
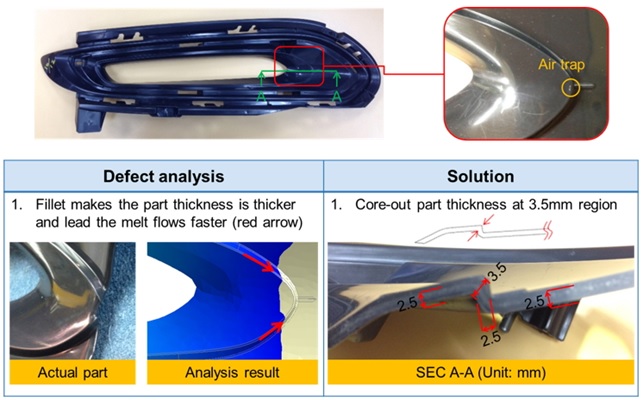
Fig. 8 Analisi e soluzione dei difetti
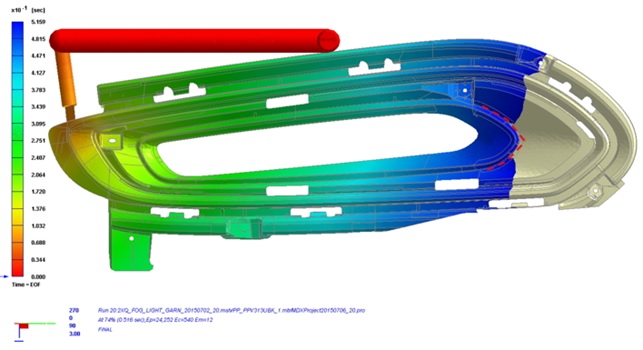
Fig. 9 Schema di riempimento del modello core-out
Il nuovo design del core-out è stato utilizzato per modificare lo stampo.
I problemi della trappola d'aria e della linea di saldatura vengono nuovamente verificati dopo la prova dello stampo e il risultato è coerente con i risultati della simulazione precedente. La trappola d'aria può essere eliminata eseguendo il core-out dello spessore della parte e le linee di saldatura aggiuntive sono accettabili poiché si trovano in regioni non visibili (Fig. 10).
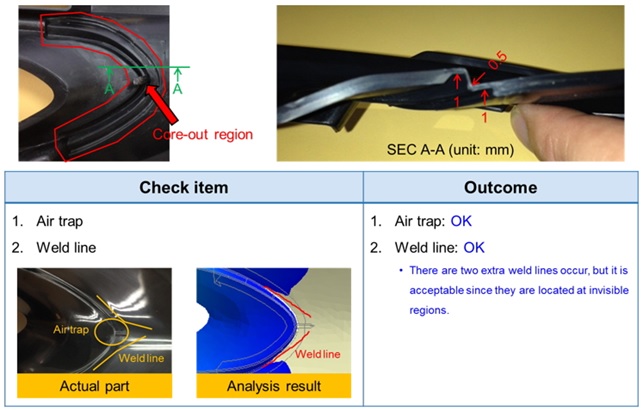
Fig. 10 Implementazione e convalida della soluzione
Risultati
La simulazione con Moldex3D è stata utilizzata fin dall’inizio del progetto e continuata durante le successive verifiche (sistema di alimentazione, punti di iniezione, ecc) e nell'analisi dei difetti dopo la prova dello stampo.
I risultati della previsione della progettazione del punto di iniezione finale sono costantemente riferiti a campioni effettivi di breve durata dopo la prima prova dello stampo.
Tuttavia, lo spessore irregolare della parte causa un problema di intrappolamento d'aria.
L’utilizzo del venting non è possibile in questo caso poiché la posizione della trappola d'aria è sulla superficie estetica.
La simulazione Moldex3D è stata nuovamente utilizzata per analizzare il difetto e convalidare la soluzione core-out nello spessore della parte per evitare costose rilavorazioni dello stampo.
Infine, Moldex3D ha assistito Tong Yang nell'ottimizzazione dello spessore delle pareti per risolvere le trappole d'aria, risolvendo con successo problemi estetici in questa parte del fendinebbia.