Come ottenere la migliore corrispondenza tra gli elementi della mesh in ambiente MCM Multi-Componente per raggiungere l'analisi ad alta precisione.
L’ambiente dello stampaggio materie plastiche è per definizione un ambiente dove son presenti molti componenti, siano essi parti dello stampo, inserti dello stampo o inserti in cavità.
L’obiettivo generale è quello di ottenere alla fine un processo di stampaggio migliore ed efficiente.
Possiamo trovare parti componenti diverse dello stampo, inserti in metallo speciale ad alta efficienza, dispositivi complessi (camere calde), inserti in cavità, di metallo o altro materiale (es. sovrastampaggio), dove il tutto concorre a costituire un unico assieme: lo stampo.
Moldex3D fornisce una potente funzione che consente la generazione automatica della mesh e crea una maglia corretta sia della parte, dell’inserto e altri componenti di stampaggio.
La nuova versione di Moldex3D R14 è in grado di sostenere l'analisi dell’ambiente multicomponente meshato in tecnica NMM (Non-Matching Mesh) tra la parte, l’inserto parte. L’inserto stampo ed altri componenti. Tuttavia, per garantire risultati di analisi ad alta precisione, gli elementi di maglia sulle facce di contatto tra la parte e parte inserto devono corrispondere.
Moldex3D Designer BLM fornisce funzioni avanzate per cucire automaticamente i vari elementi in modo che gli utenti evitino una pesante fase di operazioni manuali. Come risultato, gli utenti risparmiano molto tempo nel processo utilizzo.
I passi seguenti mostrano come comportarsi con una maglia con elementi non corrispondenti in tecnica NMM.
1. Al punto 1, si importano la cavità e la parte inserto in BLM Designer. Fare doppio clic sul componente per modificare il suo attributo (la cavità è in giallo, l'inserto parte è in rosso).
Al punto 2 e 3, si prepara il modello MCM, con il suo sistema di alimentazione (Runners e Gates) e di raffreddamento, simile a quello per lo stampaggio ad iniezione convenzionale (IM).
Al punto 4, si definiscono e/o modificano i nodi della maglia e i parametri BLM prima della generazione della mesh.
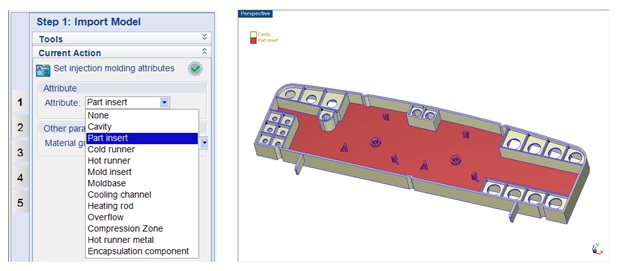
2. Ci si assicura di deselezionare l'opzione Passa alla Auto-maglia della griglia, se il sistema di raffreddamento generazione di mesh solido dovesse fallire (Proprietà del modello/Opzioni).
Così, Designer BLM può garantire la cosistenza degli elementi della maglia sulle superfici di contatto in modo tra la parte e parte inserto ci sia il corretto abbinamento per la generazione di mesh.
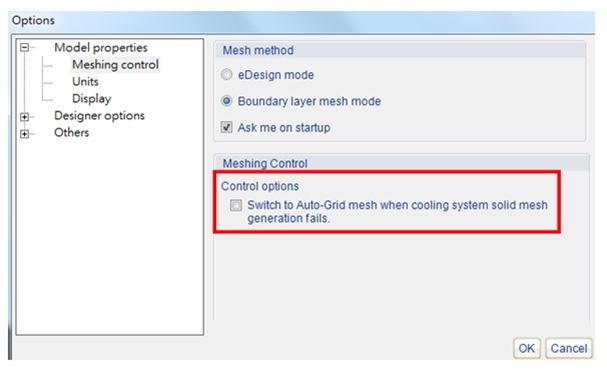
3. Si avvia la generazione di mesh. Ed il sistema provvederà automaticamente ad abbinare gli elementi di maglia sulle superfici di contatto.
Nota: Se non ci sono difetti critici rilevati dal programma, l'intero processo di meshing sarà fatto automaticamente (Generate mesg). Tutti gli elementi di maglia non corrispondenti vengono visualizzati in colori diversi per rendere più facile la loro identificazione, prima e dopo l’abbinamento.
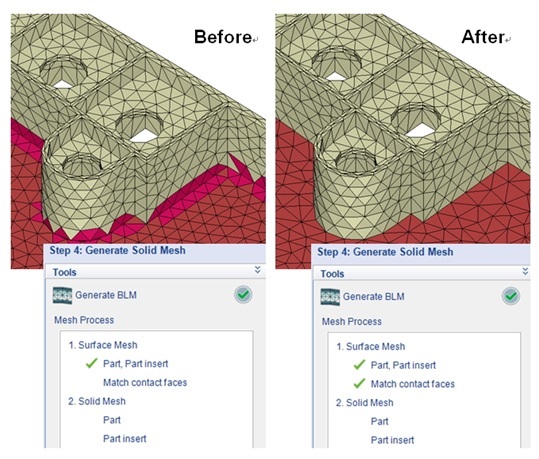
Nota: Se ci sono difetti critici rilevati nel mesh di superficie, il programma chiederà se gli utenti vogliono utilizzare gli strumenti di fissaggio / miglioramento mesh di superficie per risolverli (Fix/Enhance).
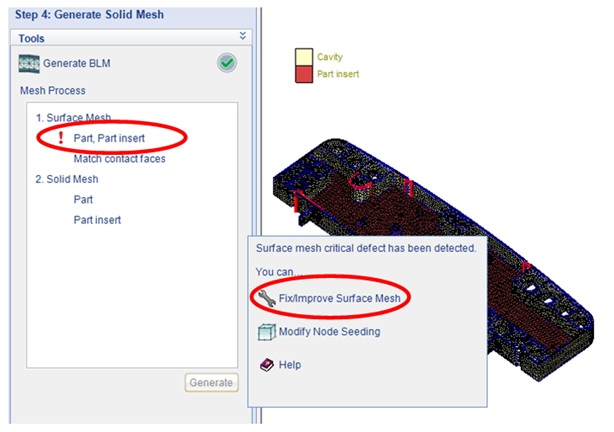
Dopo che i difetti critici sono stati corretti automaticamente dal software, fare clic su Genera di nuovo per continuare il processo di meshing.
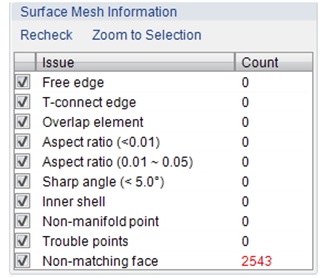
4. Una volta che le superfici di contatto sono abbinati con successo, l’ultimo passo si completa con la generazione della mesh solida per la parte e parte inserto come illustrato in figura.
Gli utenti possono quindi esportare il modello di maglia al punto 5 per ulteriori applicazioni di analisi.