Moldex3D aiuta la Dr. Schneider a elevare il design automobilistico delle parti interne
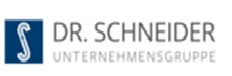
La Dr. Schneider è specializzata in prodotti in plastica di alta qualità per l'automobile, da innovativi sistemi di ventilazione a coperture interne altamente integrate e moduli sofisticati per pannelli di strumenti e consolle centrali non solo estetici ma anche funzionali. (Fonte: www.dr-schneider.com)
Ambiente e configurazione
• Cliente: Dr. Schneider
• Paese: Poland
• Industria: Automotive
• Solutione: Moldex3D Advanced; Flow, Pack, Cool, Warp, MCM, Digimat-RP, Fiber, FEA Interface, Expert, Advanced Hot Runner, Viscoelasticity, CADdoctor
Sommario
Przemyslaw Narowski, CAE Engineer del Dr. Schneider spiega come la necessità di un processo di simulazione dello stampaggio a iniezione sia emersa all'interno della sua azienda e perché sia stato scelto Moldex3D.
Moldex3D è utilizzato nello studio di fattibilità di parti di nuova progettazione e l'uso esteso delle altre soluzioni di simulazione di Moldex3D amplia le capacità tecniche dell’azienda e le Sue prospettive future garantendo per l’ingegneria e lo sviluppo prodotto un flusso di lavoro semplificato da CAD, CAE a CAM.
In questo report, vengono mostrati diversi casi reali per illustrare l'accuratezza dei risultati e dei valori di Moldex3D.
Le sfide
• Difetti superficiali causati da trappole d'aria
• Problematiche estetiche dovute alle linee di giunzione
• Trovare un'efficace ventilazione della cavità
Le soluzioni
Nel caso di una parte di riempimento, Moldex3D viene utilizzato per ridurre la quantità di deformazione del 40% per garantire la precisione dimensionale. Moldex3D ha anche contribuito a eliminare le trappole d'aria sulla superficie di una parte interna dello stampato per il settore automobilistico.
Benefici
• Testare nuovi progetti per verificare la fattibilità in stampaggio delle parti, ad esempio le posizioni dei gate ideali e il tempo di ciclo stimato
• Risolti problemi di stampaggio difficili, come la deformazione (del 40%) e le trappole d'aria.
• Ispirare il concetto di "Reverse Simulation" per la direzione futura dello sviluppo di prodotto
Argomento di studio
L'obiettivo principale è quello di convalidare l'accuratezza dei risultati della simulazione Moldex3D rispetto a casi sperimentali reali e prevenire ulteriormente problematiche di deformazione e trappole o bruciature visibili sul prodotto.
Nel primo caso, Schneider ha utilizzato Moldex3D per simulare il comportamento di deformazione di un elemento di guida (Fig. 1) e la leva della cabina del bocchettone Fig. 2) e ha trovato che i risultati della simulazione corrispondono ai risultati dell'esperimento fisico
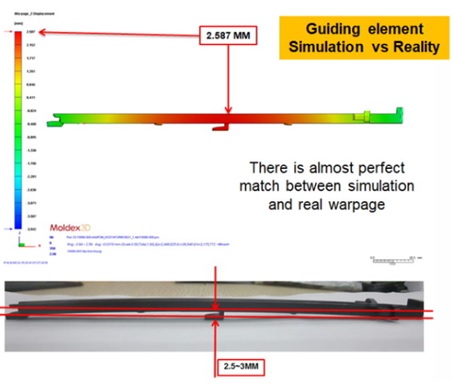
* La corrispondenza tra simulazione e vera deformazione è quasi perfetta
Fig. 1 I risultati della deformazione della simulazione e della realtà dell'elemento guida

Fig. 2 Il risultato dell'analisi della deformazione rispetto alla misurazione reale
Nel secondo caso, sono state previste eccessive deformazioni e trappole d'aria nella leva del bocchettone di rifornimento e nel suo coperchio usando Moldex3D.
Questi potenziali problemi potrebbero causare difficoltà ed errori nell'assemblaggio e influenzare l'aspetto estetico della parte.
Con l'aiuto di Moldex3D, Schneider ha sviluppato un nuovo design, che ha ridotto di metà lo spessore del materiale nell'area del restringimento massimo della metà (Fig. 3) e ha identificato le posizioni di ventilazione e sfogo d’aria adeguate (Fig. 4).
Di conseguenza, la predizione ha mostrato che lo spostamento totale della deformazione era significativamente migliorato.
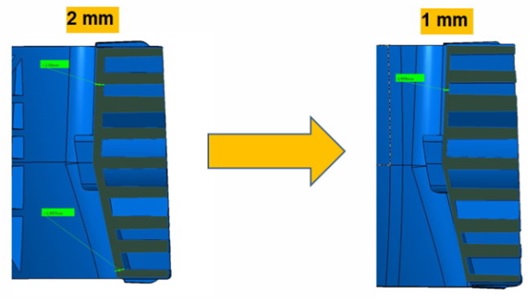
Fig. 3 Il design ottimizzato ha ridotto di metà il materiale nell'area del restringimento massimo e migliorare la deformazione totale
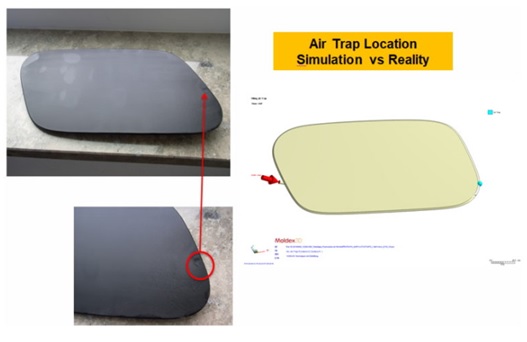
Fig. 4 Moldex3D è in grado di prevedere con precisione la posizione delle trappole e identificare le posizioni di ventilazione adeguate.
La Dr. Schneider ha utilizzato Moldex3D per simulare il design originale e il design ottimizzato. Il risultato dell'analisi del progetto originale ha mostrato che un elevato ritiro si sarebbe verificato nelle aree spesse della parte (Fig. 5) e provocato, conseguentemente, un'eccessiva deformazione.
Dopo aver modificato lo spessore della parte, la previsione ha mostrato che lo spostamento della curvatura è stato ridotto di quasi il 40% (Fig. 6).
Fig. 5 Un'eccessiva distorsione è stata prevista nel progetto originale
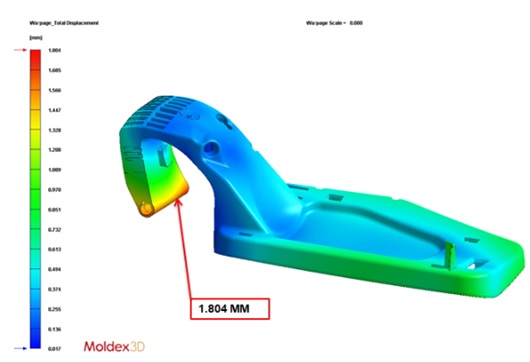
Fig. 6 Lo spostamento totale della deformazione è stato rosso
I risultati
Attraverso l'analisi Moldex3D, la Dr. Schneider ha compreso chiaramente il comportamento di riempimento e deformazione ed è stato in grado di prevedere potenziali difetti prima della produzione effettiva.
Al giorno d'oggi alla Dr. Schneider, Moldex3D è uno degli strumenti più importanti utilizzati negli studi di fattibilità nella fase di sviluppo del prodotto.
Ogni disegno stampato ad iniezione deve passare attraverso l'analisi di riempimento dello stampo. Se qualcosa va storto, ad esempio, quando i valori di deformazione non sono accettabili, il team del Dr. Schneider intraprenderà azioni correttive.
Alla fine, il Dr. Schneider è in grado di risolvere con successo i problemi di produzione e ottimizzare i progetti di stampi e prodotti, che li aiuta a ridurre in modo efficiente le prove di stampo e i costi di modifica dello stampo prima della produzione effettiva, nonché di accorciare i tempi i risposta alla richiesta del Cliente finale.
Moldex3D ITALIA – Giorgio Nava prt. 2018_0027