Industry 4.0
Simulazione dello stampaggio e Smart Manufacturing con Industry 4.0
Capitolo 2: Smart Injection Machines e loro principi di regolazione
Dal concetto di integrazione di virtualità e realtà in Industry 4.0, menzionato nel capitolo precedente, abbiamo capito che il movimento della macchina, con le sue inerzie meccaniche, è molto rilevante per la qualità del prodotto in un processo di stampaggio ad iniezione.
Per ottenere un'accurata analisi di riempimento dello stampo, dobbiamo considerare i movimenti della macchina, tra cui l'accelerazione e decelerazione della vite in fase di iniezione, la reazione della macchina nel momento in cui il riempimento si trasforma in compattamento (post- compressione).
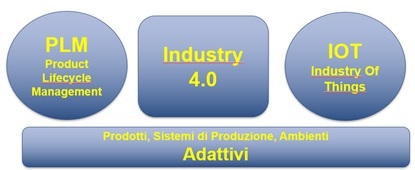
Si aggiungono anche comportamenti di protezione della macchina per evitare che la pressione di iniezione sia troppo alta.
Attualmente, il cuore delle attrezzature di stampaggio in ambiente plastica sono le macchine a iniezione.
Una percentuale più piccola, almeno per ora, riguarda altri processi: Compressione, Gas, Inietto-compressione, ecc. fino ai processi più complessi RTM (Resin Transfer Molding), microcellulare, o SMC (Sheet Molding Compound).
Pertanto, nell'ambito di Industry 4.0, le applicazioni delle macchine intelligenti si concentrano principalmente sulla progettazione di macchine a iniezione.
Le applicazioni includono:
1. La macchina a iniezione invia i dati di gestione della produzione;
2. Lo scambio di dati tra la macchina ad iniezione e le macchine ausiliarie periferiche;
3. La regolazione intelligente del processo di stampaggio.
La regolazione intelligente del processo di stampaggio determina in particolare il futuro delle industrie dello stampaggio ad iniezione.
Il motivo è, fino ad ora, che lo sviluppo in questo settore si basa ancora fortemente sull'esperienza delle persone.
Va da sé che, né l'analisi del riempimento degli stampi, né le macchine intelligenti possono sostituire l'esperienza delle persone.
E’ la combinazione tecnologia+esperienza che crea le condizioni per una vera soluzione.
Tuttavia, l’insieme di tecnologia+esperienze e l’organizzazione aziendale (raccolta delle informazioni sulla produzione, gestione dei dati in ingresso ed uscita, regole e protocolli industriali) portano verso quello che possiamo definire
“stampaggio automatico”.
In questo articolo, prenderemo in considerazione come i produttori di macchine a iniezione applicano le informazioni, raccolte dal processo di iniezione, per migliorare la stabilità della qualità del prodotto.
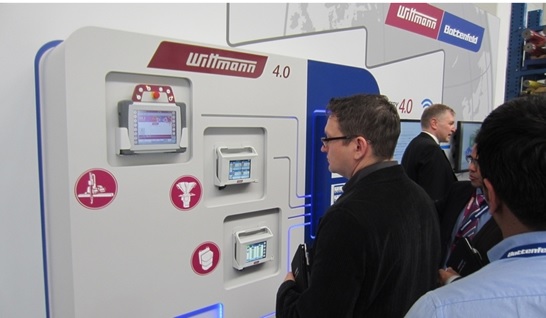
Per aumentare la stabilità della qualità del prodotto, possiamo regolare adeguatamente i parametri di stampaggio per compensare l'instabilità della qualità causata dalla variazione ambientale.
Sulla base della loro esperienza, i professionisti dello stampaggio sanno che a volte dovevano adeguare i parametri di stampaggio per compensare gli effetti della temperatura dell'ambiente al mattino e alla sera, nonché in estate e in inverno.
Il concetto di macchine intelligenti è quello di modificare direttamente le condizioni di stampaggio in ogni ciclo di stampaggio attraverso metodi scientifici.
Attualmente, quasi tutti i produttori di machine di stampaggio si stanno indirizzando su questa strada; tra questi Engel (controllo del flusso iQ), Wittmann Battenfeld (HiQ-Flow) e KraussMaffei (APC).
Prendiamo ad esempio Battenfeld HiQ-Flow, che costituisce un esempio di Applicazione di Sistema IOT (Internet of Things)
WB ha definito un protocollo WB Industry 4.0 di inter-connettività, interna ed esterna, che permette alla stazione di lavoro di:
• raccogliere dinamicamente i dati tramite una rete di sensori,
• automodificare (morphing) i parametri di stampaggio e di uso della stazione (es.consumo energetico, temperature, ecc.) per un processo ottimale,
• comunicare direttamente con il centro di controllo aziendale (ovunque esso sia) e con il centro di supporto WB di Kottingbrunn (A), senza soluzione di continuità.
HiQ-Flow agisce in modo articolato, impostando i limiti superiore e inferiore della variazione della pressione di iniezione della gamma di prodotti qualificati.
Ciò permette di monitorare la pressione di iniezione, ovvero prendendo come standard la curva di pressione di iniezione.
Se lo stampo, la viscosità del fuso e la pressione di iniezione rimangono tutti uguali, la pressione di iniezione non cambia (stabilizzazione).
Tuttavia, se l'ambiente dello stampo (es.: il bilanciamento del sistema di alimentazione (runners) di uno stampo a cavità multiple, o la temperatura dello stampo, o la viscosità del fuso (uniformità della temperatura del fuso, degradazione e differenza di lotto) cambiano, la curva di pressione di iniezione si posizionerà fuori dal range previsto per quel deteminato prodotto, e il Sistema rileverà l’anomalia e interverrà, cercando di evitare di avere un prodotto “instabile” e quindi fuori dai parametri qualitative prescritti.
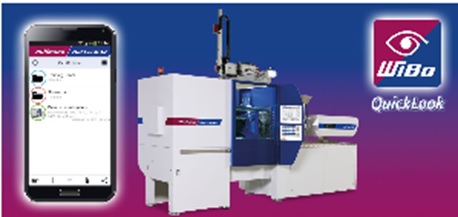
La pressione di iniezione è il prodotto di velocità di taglio e viscosità.
Se osserviamo la diminuzione della pressione di iniezione, mentre la velocità di iniezione della macchina rimane la stessa, significa che la viscosità del fuso è diminuita.
Di solito, questo fenomeno è causato dall'aumento della temperatura.
Nel frattempo, la densità del fuso diminuisce a causa della temperatura più elevata.
Pertanto, se si desidera mantenere lo stesso peso del prodotto, il volume/tratto iniettato dovrebbe aumentare o il punto di commutazione VP dovrebbe essere posticipato.
Quanto deve essere differito dipende da quanto questa pressione di stampaggio devia dalla linea standard dei prodotti qualificati.
I produttori di macchine per iniezione hanno diversi metodi per affrontare questo problema.
Il Sistema di adeguamento di Battenfeld dipende dall'uguaglianza di pressione e dall'area totale considerata, cioè dall'uguaglianza del lavoro di iniezione durante il processo di iniezione.
Il Sistema di adeguamento di KraussMaffei considera la compensazione delle proprietà PVT.
Significa che la densità del materiale (volume specifico) cambia al variare della temperatura, sapendo che la pressione di iniezione è diversa dalla linea di base.
Per compensare la variazione di densità del materiale, dobbiamo modificare il punto di commutazione VP e la pressione di riempimento in modo che il peso del prodotto possa rimanere lo stesso.
Utilizzare questo metodo richiede l’inserimento, nell’interfaccia dati del controller, del tipo di plastica utilizzato, in modo che la relazione PVT corretta possa essere così decisa in riferimento alla sua banca dati.
La seguente tabella reassume, in modo molto sintetico, la tecnologia di adeguamento del processo di alcuni produttori:
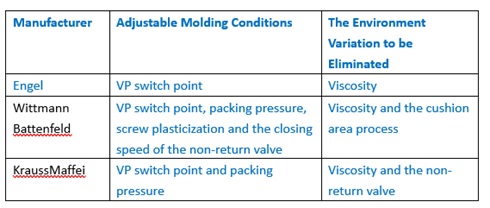
Possiamo capire che la macchina a iniezione si è trasformata da semplice “fornitore di energia cinetica” ad un Sistema che, pur matenendo elevate caratteristiche meccaniche, è diventato più complesso e sofisticato dotato di diversi sensori attivi e passivi.
Possiamo anche capire in che modo il fuso viene iniettato nello stampo per poter aggiustare ulteriormente il processo in ragione dei comportamenti comportamenti del fronte del fuso a diversa temperatura e pressione.
Questo ci aiuta a raggiungere l'obiettivo di realizzare una macchina intelligente.
L'adeguamento immediato durante la produzione può essere realizzato come "Produzione predittiva".
Secondo il Dr. Jay Lee, per produzione predittiva non significa solo creare valore per la produzione, ma anche aggiungere la funzione di "introspezione" al processo di produzione.
In altre parole, l'intero sistema, compresa l'apparecchiatura stessa, deve intraprendere azioni immediate ai cambiamenti del processo di produzione per ottenere il miglior prodotto.
In un incontro dello scorso anno, il dott. Jay Lee, che ha appena assunto la carica di vicepresidente di Foxconn Industrial Internet (FII), ha detto che “la produzione intelligente non è nata per risolvere problemi, ma è nata per percepire e prevedere i problemi e risolvere i problemi che non siamo riusciti a risolvere in passato”.
Pertanto, possiamo dire che l'era di Industria 4.0 è l'era della produzione predittiva.
Dr. Tober Sun
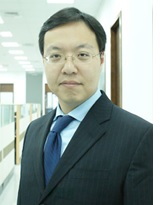
Direttore presso Material Research Center of CoreTech System (Moldex3D)
Con un dottorato in Polymer Science presso l'Università del Connecticut, il Dr. Sun si è specializzato nella ricerca di materiali compositi, biomedicali, polimeri degradabili, applicazione di materiali plastici in progetti industriali, reologia dei polimeri, elaborazione dei polimeri e proprietà fisiche dei polimeri. È stato Responsabile della Divisione Supporto Tecnico Moldex3D e Progetto Automotive ed è docente a lungo termine dei corsi e seminari professionali globali di Moldex3D
MDXITA – prt2019_0031- Giorgio Nava